When converting from plastisols to water-based inks, there are three important things to consider:
- Select a water resistant emulsion and ensure that it is properly exposed
- Keep the ink on the screen wet and
- Ensure that you have adequate curing capacity
EMULSION
You can get away with all sorts of screen prep short cuts when printing with plastisol, but many short cuts will be exposed once you start printing with water-based inks, so greater care is essential.
You MUST have a water-resistant emulsion, the emulsion must be completely dry before exposure (keep a humidity meter [hygrometer], plus a dehumidifier and a fan in the dark room/screen storage room) and then thoroughly exposed to achieve full cure before printing. Moisture in the film, even re-absorbed humidity, will reduce efficacy of UV cure on exposure and the integrity of the cured film will be compromised and thus more likely to break down, particularly on longer print runs.
For your screen storage room, keep the humidity between 30 and 40 % RH, keep the temperature between 18 °C and 29 °C and ensure good air circulation. Keeping RH within the band is important. RH above 40% is likely to lead to excessive moisture reabsorption and thus poor cure, whilst RH below 30% can lead to embrittlement of the emulsion to the extent that it flakes off during rinse out. Everything in balance.
With a water-based ink, particularly on long runs, a poorly cured emulsion will result in premature failure/shredding of the emulsion/stencil image and that will result in extra costs.
The first indication of premature failure will be a slight sweatiness on the underside of the screen. This can be felt with the back of the hand when the screen is up between prints. The second indication is pin-hole failure of the stencil, resulting in unwanted dots appearing on the printed image. If this happens, stop printing immediately. The third indication is that the emulsion starts to shred.
So, to prevent premature stencil failure:
- Choose a WATER-RESISTANT emulsion and block-out
- Ensure that the film is fully dried before exposure and
- Ensure that the film is fully exposed or cured
KEEP INK WET ON THE SCREEN IMAGE
This is arguably the greatest challenge for plastisol printers when converting to printing with water-based inks. First and foremost, keep the image area flooded between prints.
When printing on white fabrics with PERMASET Standard (transparent) inks, keeping the screen open is relatively easy. However, with the much higher solids, opaque HSAs like PERMASET SUPERCOVER Inks, significantly more care is required.
It is also worthwhile to have another hygrometer in the print area. When printing with water-based inks, it is good practice to maintain RH above 40%, or even 50% with HSAs and finer meshes. However, whilst high humidity over the screens is great for water-based ink maintenance, it can lead to other problems around the shop (see below).
Before starting your print run, ensure that you have a spritzer bottle of water handy. Give the image area a really good misting over and allow this to soak in for 10 minutes. This water is absorbed into micro-pores and other interstices in the polyester mesh fibre matrix. This does 3 things; first, it stops the very limited “free” water in the ink being sucked out of the ink at the start of the print run. Second, it provides a lubricating film of water over the fibres, allowing the ink to flow more smoothly over the mesh. Third, it acts as a reservoir of water from which the ink can draw during the course of the print run.
After the 10 minute soak, wipe off any excess moisture, put ink on the screen and get ready to start printing. Turn off your phone and don’t stop whilst printing! The less time between prints, the less will be the opportunity for ink to dry in on the screen. This is most acute with HSAs and/or with high mesh counts.
If you are interrupted for a relatively short period, flood the image area with ink and spray mist liberally over the wet surface. If the interruption is likely to be lengthier, then spray mist liberally over the wet ink surface and then put cling-film over the wetted surface to minimise evaporation. Best practice is to change set up to avoid interruptions.
It is also worth noting that ambient conditions, in particular humidity, can change dramatically during the course of a day, particularly during long print runs and that these changes can affect the behaviour of water-based inks a lot more than plastisols.
In a city like Denver, Colorado, where RH is likely to be low, a set up that works brilliantly in the morning can fall off a cliff in the afternoon as humidity drops. Thus, it is important to be alert to the conditions and be prepared to tweak the set up as local conditions dictate.
DRYING & CURING
With plastisols, if, having gone through the drying tunnel, the print looks dry and feels dry, then you can be pretty sure that it has cured. With water-based inks, the drying and curing steps are separate. First, ALL the water has to come out, so that it feels dry and only THEN will you start to achieve full cure. Remember that a typical curing regime is 2–3 minutes @ 160°C (320°F). However, the temperature cannot get over boiling point (100°C; 212°F) until all the water has left the film. It has been calculated that 90% of the energy consumed in a drying tunnel goes into water removal; only the last 10% goes into the cross-linking or curing and it is not until the ink is properly cured that the print achieves wash and dry-clean resistance properties.
An associated issue is airflow within the drying tunnel. If air movement is poor and/or exhaust is inadequate, then the humidity in the tunnel becomes saturated, no more water can leave the wet ink film and the print doesn’t even dry, let alone achieve full curing. So it is imperative to ensure that you have adequate airflow, ideally flowing from the rear to the front, so that the driest air is at the exit end.
In humid climates, cotton T-shirts in particular may absorb a lot of moisture prior to printing, so it might be worth running the unprinted garments through the tunnel prior to printing, just to reduce the moisture removal load on the tunnel during the actual print run or keeping them under wraps until you are ready to print, or both.
If you only have a limited length drier, it may be necessary to run the garments through multiple times. An alternative is to slow the belt-speed, but this can result in slowing down the entire print operation. The best option is to invest in a good drier of adequate length with sufficient air movement and appropriate exhaust.
The above may seem overwhelming at first, but it is very doable, you will get used to it as a new normal and your customers, your staff and the planet will thank you for it! And if you do get stuck, just email us at [email protected]
© COLORMAKER INDUSTRIES 2021
Subscribe to get the latest inspiration, news & advice direct to your inbox
More articles
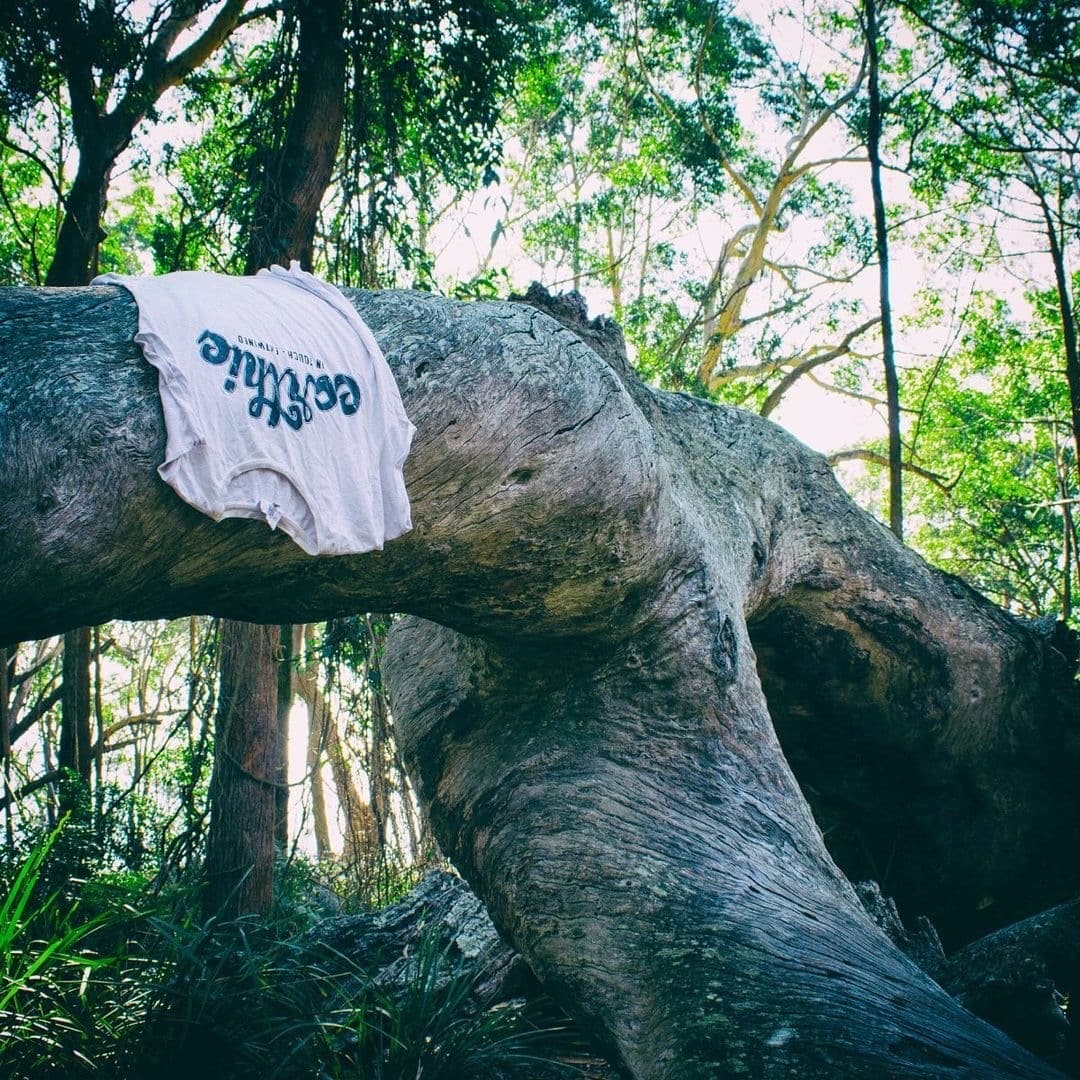
Clothing label I’m Earthie shares how they strive to be a truly sustainable brand
Clothing label I’m Earthie shares how they strive to be a truly sustainable brand