About KLT:works
Kristin Loffer Theiss started a working studio in the Pacific Northwest called KLT:works in 2005. She’s been making and designing products for the modern home & family under the KLT:works label ever since. The KLT:works studio has expanded over the last few years, including various forms of printmaking and surface design as the primary focus in the products offered. Kristin’s love of textiles, screen printing and mid-century design has influenced her new line of printed goods.
Kristin and her husband, Chris, both hold MFAs in Fine Art and met in 1996, teaching at the local college (Skagit Valley College) where they remain adjunct faculty, Kristin occasionally teaching drawing or painting & Chris maintaining a continuously full schedule of ceramics, 3-D design, drawing, gallery and art. They have a child named Sayer, who is a young artist and musician in his own right along with being the business “tech” consultant (he made & maintains their website). KLT:works is a family studio and all three creatives have their part in the success and unique vision of the business. A day in a life around their house includes laughter, dancing, listening to music and making. Everything you see with a KLT:works label is made by hands – with attention to detail and lots of heart.
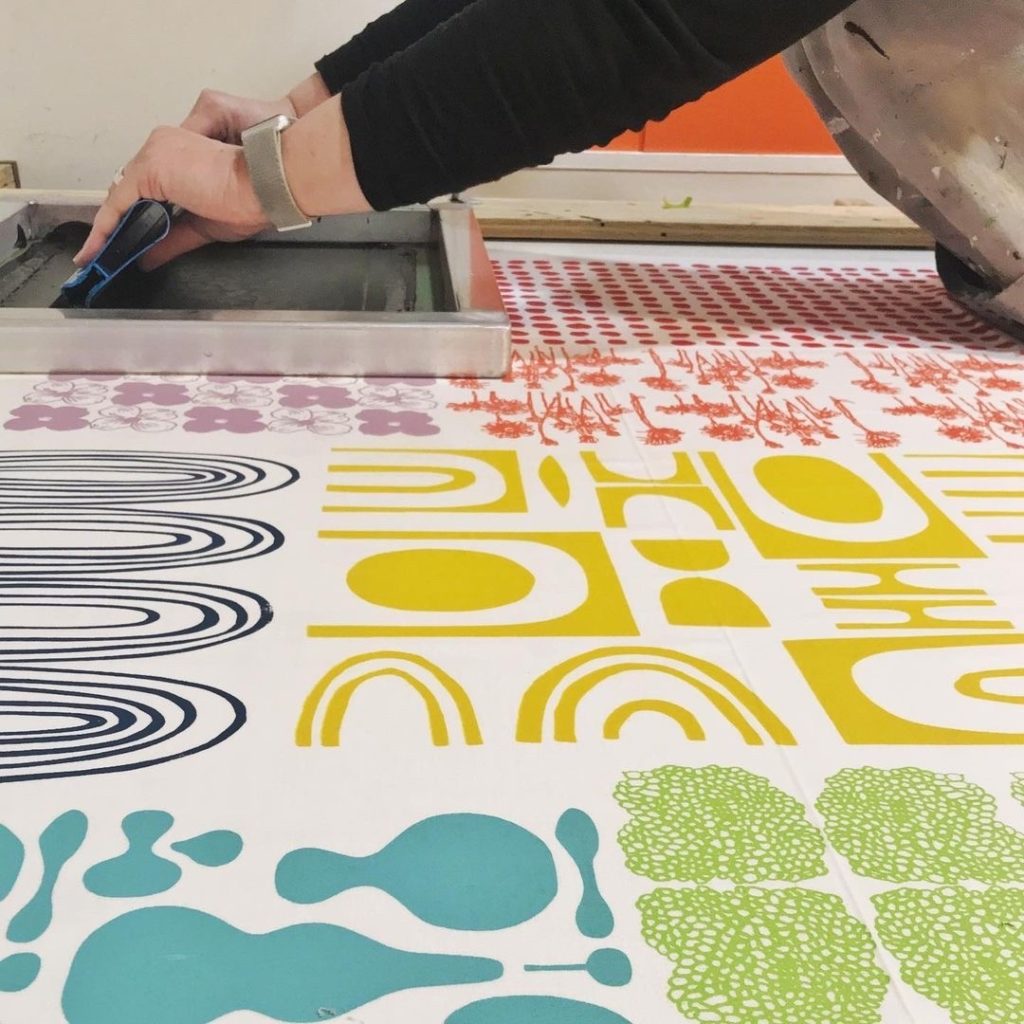
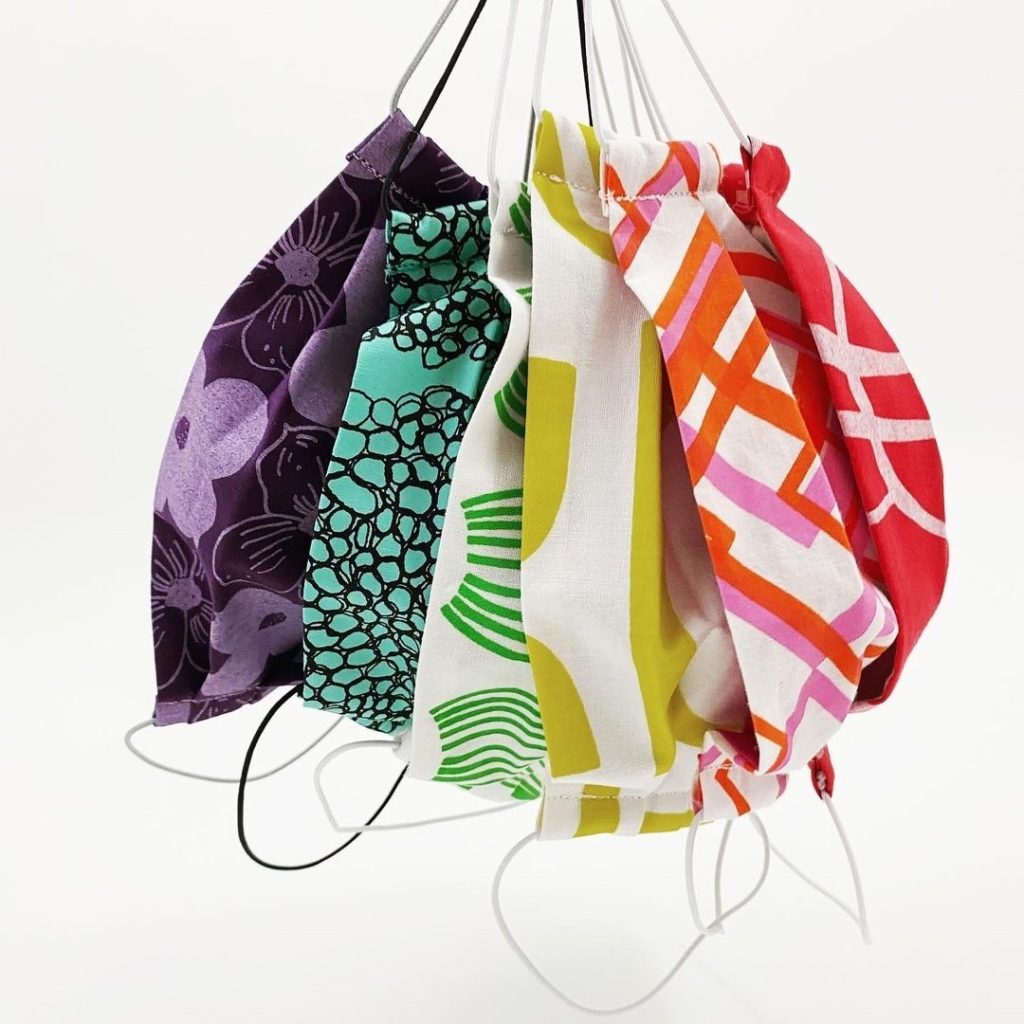
I
COVID-19 and getting resourceful
“When we were first told to Stay Home and Stay Safe due to the Covid-19 pandemic, I spent a lot of time organizing and cleaning out my studio spaces. As I was digging through stacks of fabric that I had printed years ago, I was continuously asked if I was going to make masks. So, I thought utilizing all of my new found stacks of printed fabric might be a good idea. I started making masks with a tutorial that my doctor’s office recommended – one that has a pocket for a filter and has adjustable elastics that go over the ears. I made 25 and gave them away to local nurses, front line workers and vulnerable folks in the valley. I saw it as a way of giving a hug or a little extra kindness. However, the demand was so big that I found myself making more and having to get creative when sourcing elastic. It slowly became all I was doing” said Kristin.

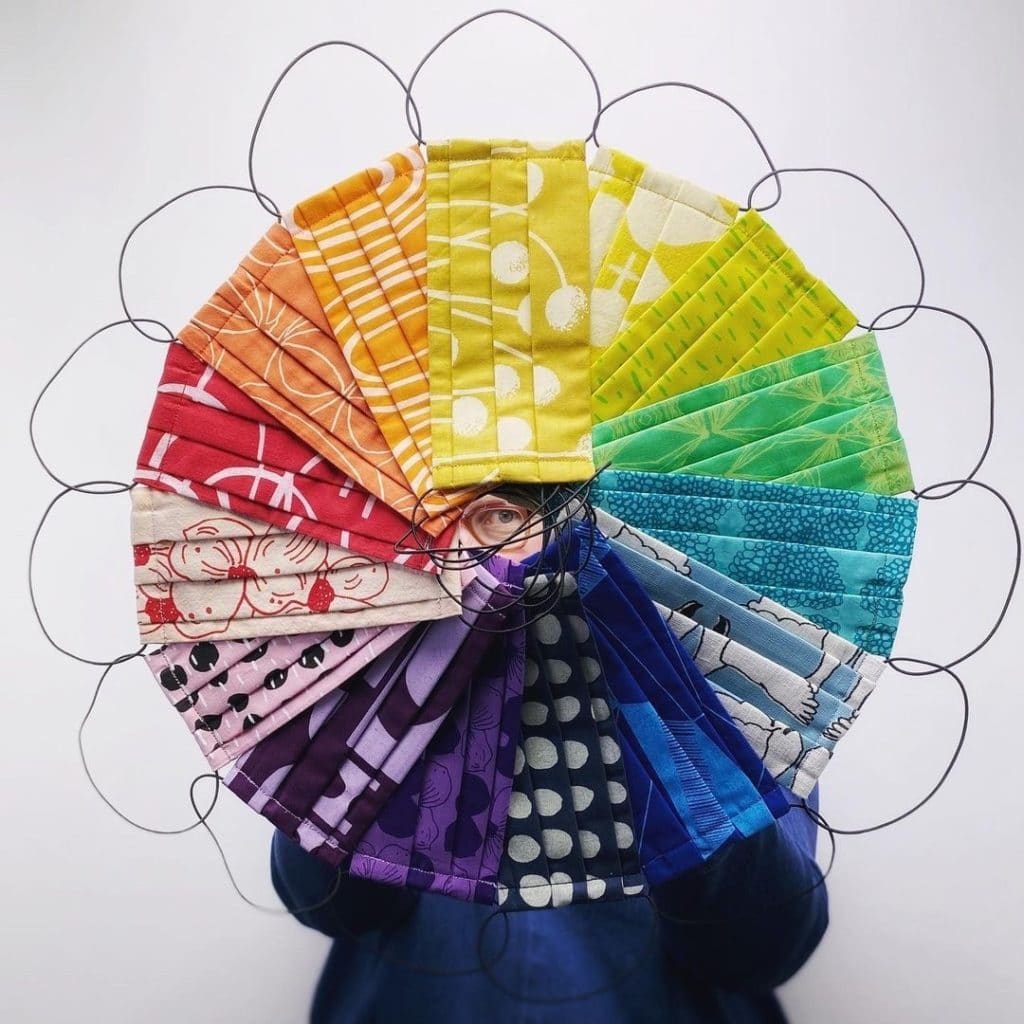
“My husband Chris and I came up with a system – he cuts and I sew. I offered kerb-side pick-up and found that it was my favourite part of the process. I get a little hop in my step when I know people are going to come pick up their masks. I love all of the conversations that I’ve had with people and it fills me up that my masks are making people smile and feel a little safer. The social worker, bleeding heart part of me eats this project up. It’s nice to feel like I’m helping just a little bit – it’s been giving me a new purpose. However, I ran out of fabric so I had to print more.”
“I decided to start printing fabric for more masks, which means I’ve committed to doing this as long as there is a demand. As I print, I’m coming up with more projects and ideas, ebbing and flowing in that creative bubble. I’m so grateful to be able to do this, it’s filling me up at a time that is a bit deflating. I printed a little variety of fabric on one yard, randomly. It was just a way to save time, but I liked how it looked before I cut it up” she advised.
“Then, I had an accident – I was rushing. If you are a chef, maker, seamstress, or just a go getter, you may have done this too. I cut off the tip of my finger with a rotary cutter. While I don’t care that I won’t ever be asked to be a hand model in my lifetime, I do care that it will slow me down for a little bit. It’s affecting my ability to print fabric and sew quickly.”
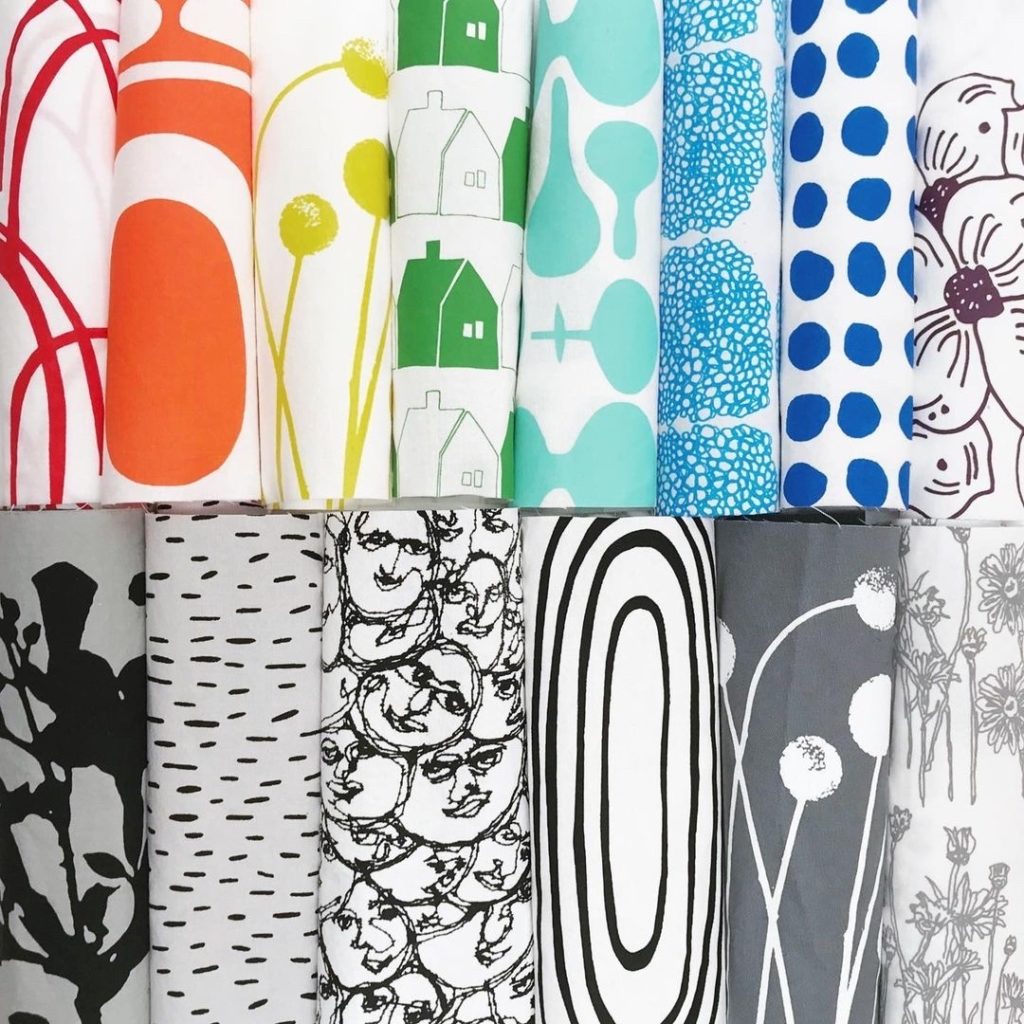
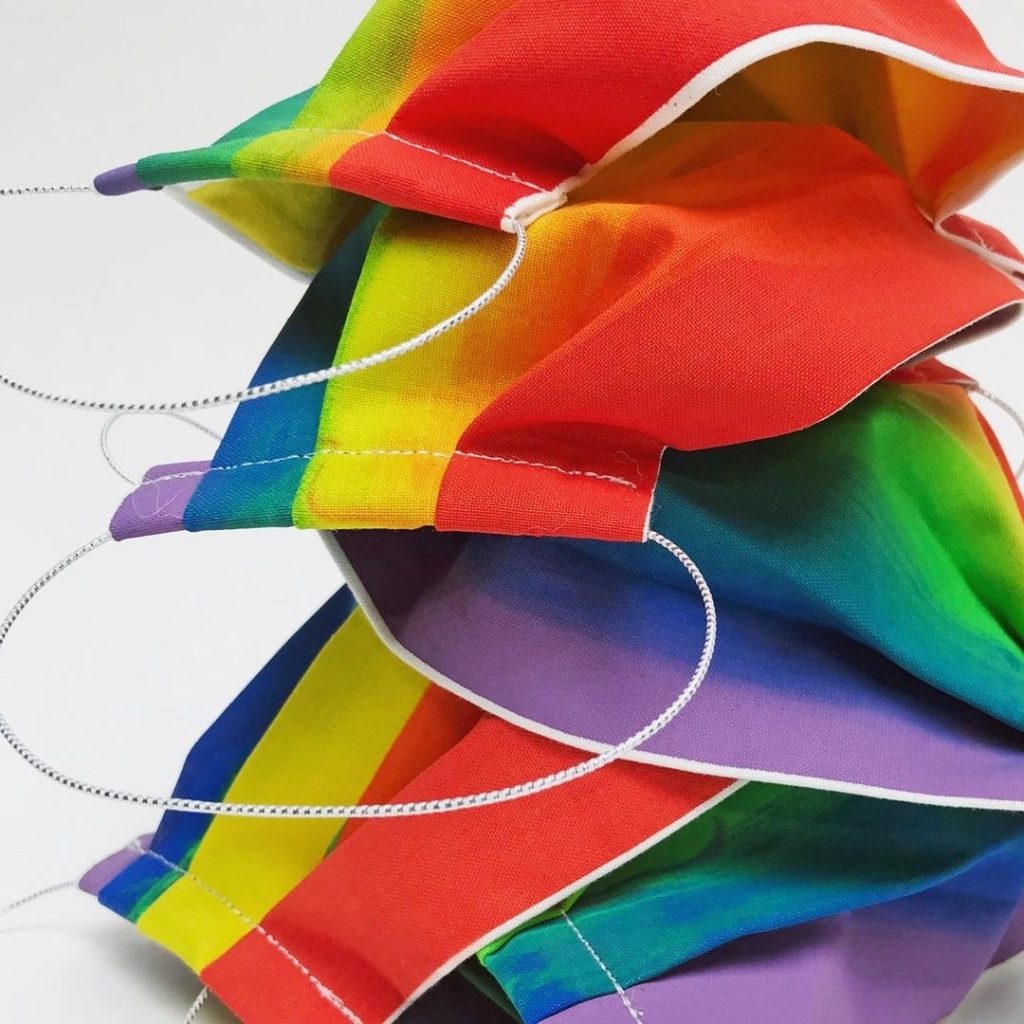
2687 colourful masks in 2020
“On April 1st 2020, I started making masks with my hand printed fabric- I made 2,687 in 2020! The original idea was to make something beautiful & unique for people during such a gloomy time. I offered the “ROYGBIV Collection” and continuously printed new colours/patterns – I organized each finished batch in a colour wheel photo to entertain myself. I’ve lost track of what mask collection this is…but it’s in the double digits” advised Kristin.
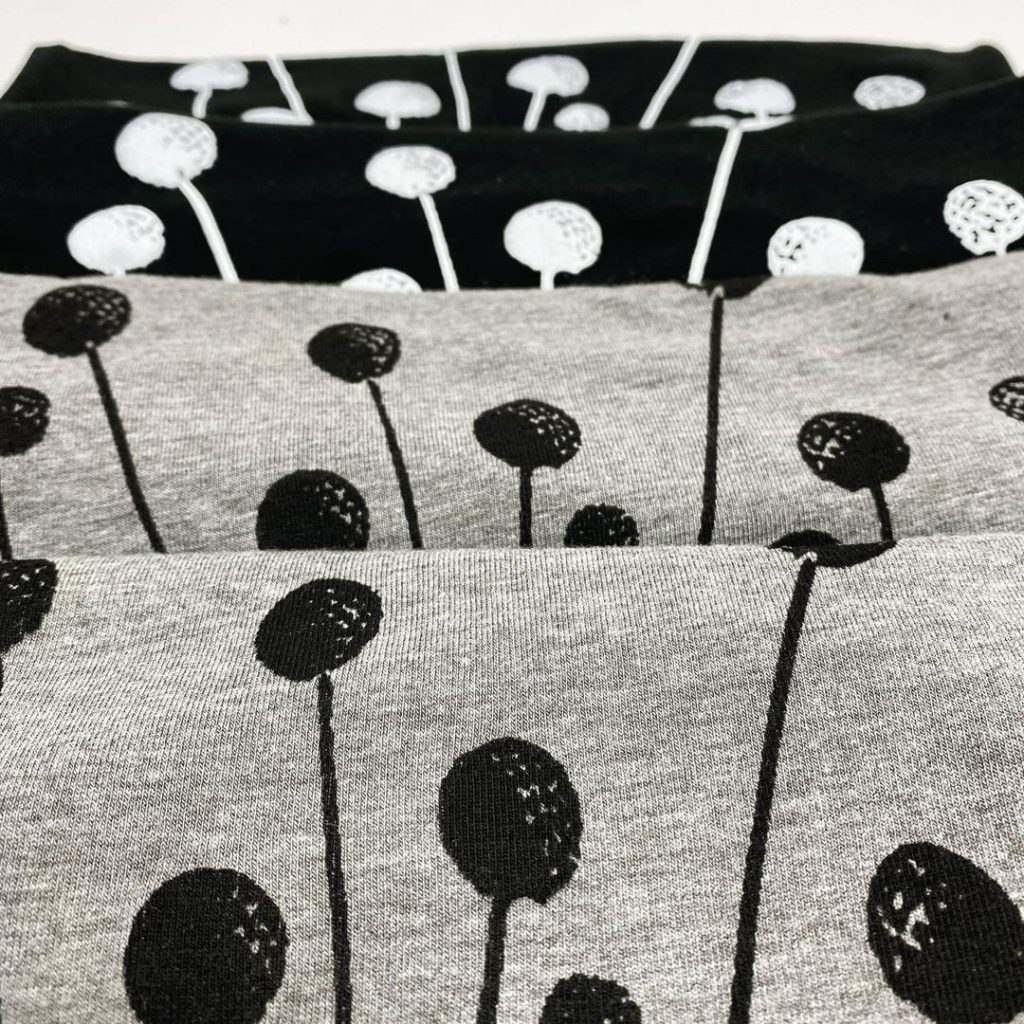
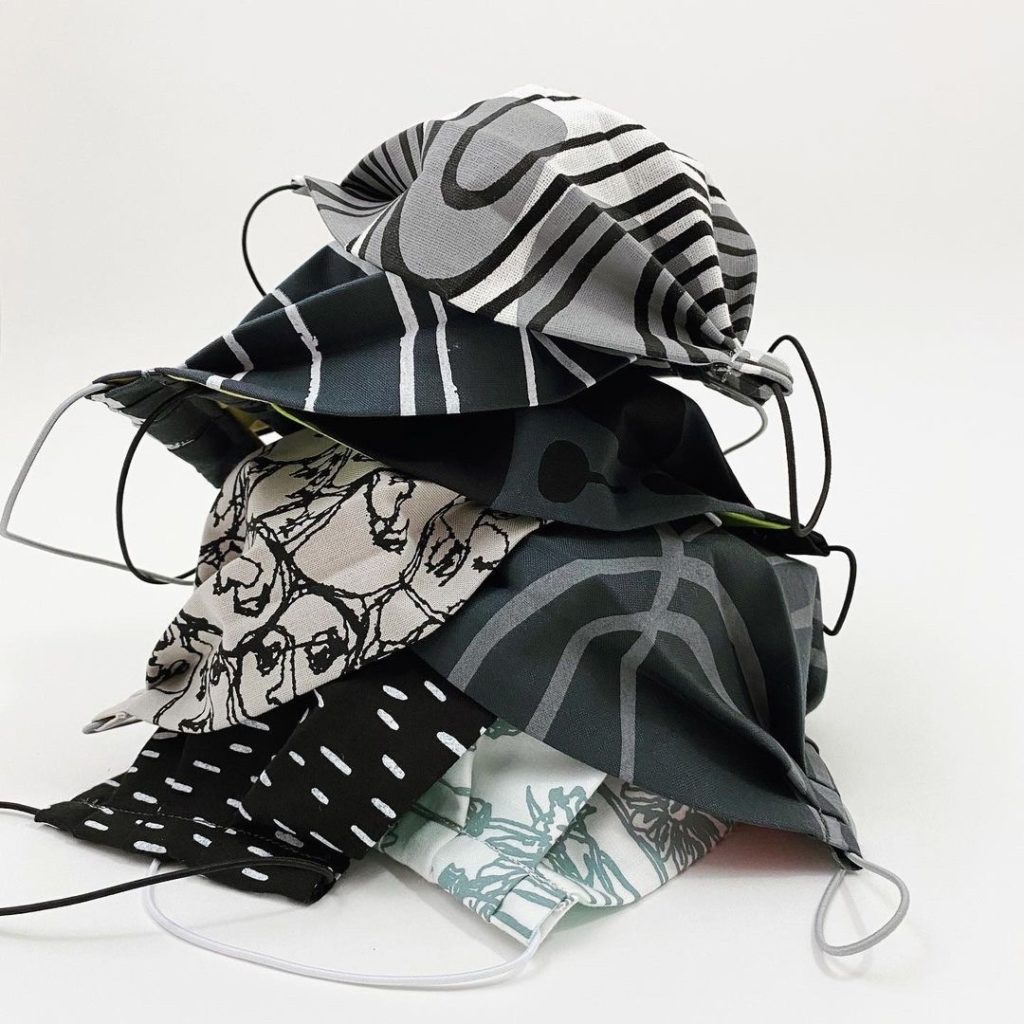
“It’s 2022 now and yes, we’re still making masks. Thanks to all who have purchased masks from me over the last few years. I really appreciate you supporting our small business. We also made some greyscale masks for those not wanting as much colour and some bandana scarves.”
“I fiddled with an idea in the studio and my guys were nice enough to be my testers.”
“All fabrics are hand screen printed by me using PERMASET eco-friendly water-based inks. These inks can be used on all types of fabrics. I made the bandanas by screen printing a design onto cotton jersey.”
Kristin even printed some masks to celebrate Pride Month in October 2021. “I printed a lot of rainbows today – it was a good day for human rights.” she said.
COPYRIGHT© Colormaker Industries 2022.
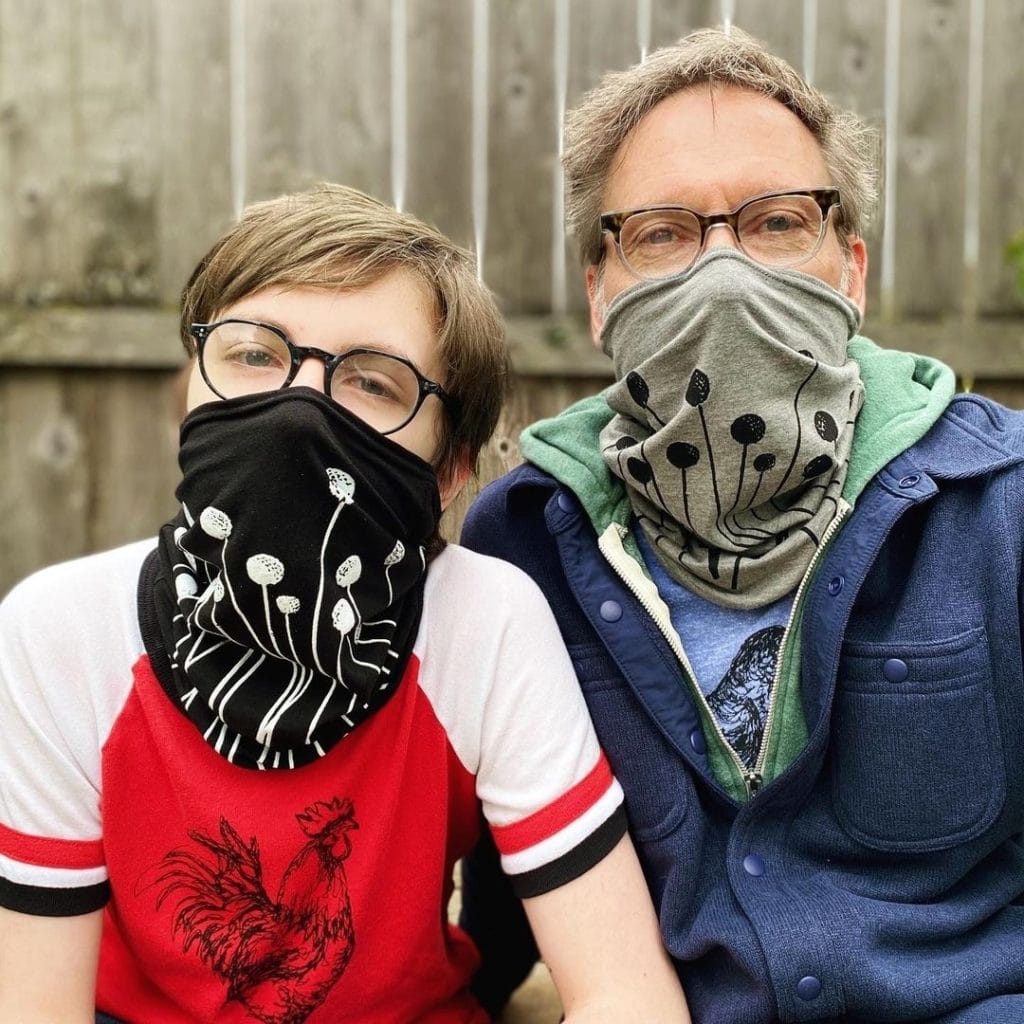
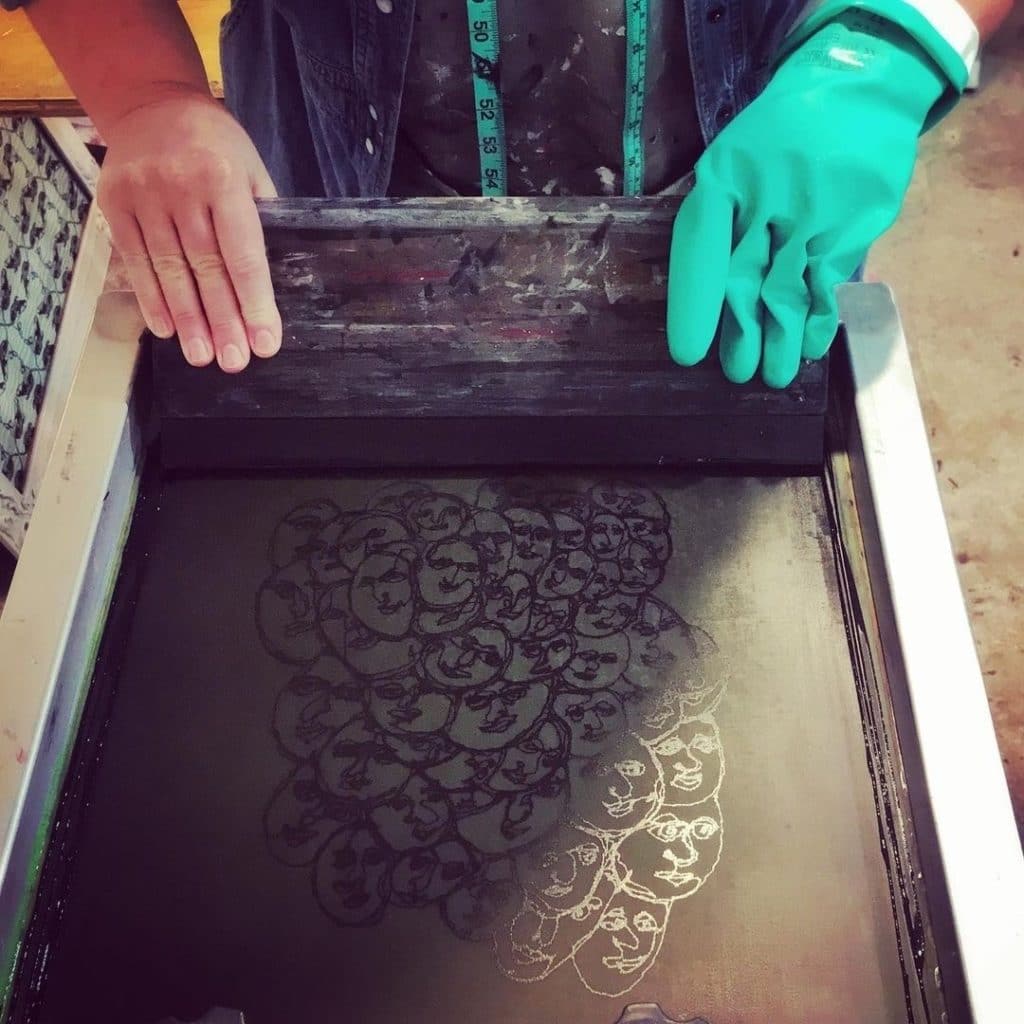
Subscribe to get the latest inspiration, news & advice direct to your inbox
More articles
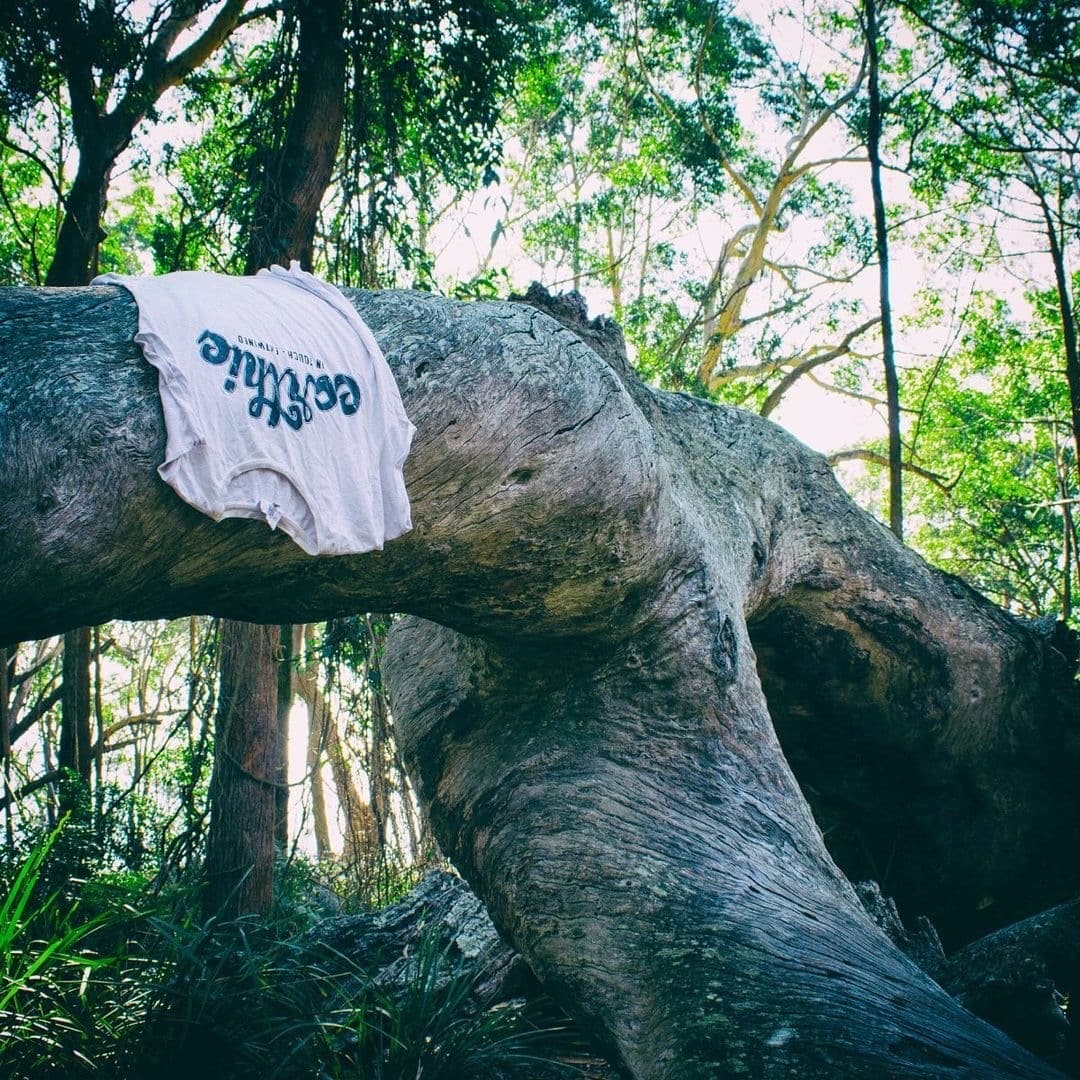
Clothing label I’m Earthie shares how they strive to be a truly sustainable brand
Clothing label I’m Earthie shares how they strive to be a truly sustainable brand