This is the second BLOG in our PRINT SHOP HYGIENE series.
If we want a safer world, then we all need to take a little more care, sometimes in just a few areas. This series on PRINT SHOP HYGIENE seeks to dive more deeply into some of those areas and highlight actions that we can all take to achieve a better tomorrow. There are a number of obvious things that come with experience, but for start-ups and studios with high turnover of personnel, like schools and colleges, that experience is not as readily available.
We’ll look at some common pitfalls of the inexperienced, together with some DOs and DON’Ts to help produce the best prints possible with the smallest environmental impact.
Old technology inks, including plastisol and the early water-based inks that contained 10–35% white spirit (distillate), were almost bullet proof when it came to microbial attack and shelf life. By comparison, while the newer water–based inks are definitely more eco-friendly, a flip side of that coin is that they can sustain microbial life and in a print studio, this is manifest as mould, fungal and bacterial infestation.
So, in much the same way as you’d need to maintain good hygiene and housekeeping practices in a food preparation area, so too in a screen printing environment. A few key housekeeping practices can help you produce brilliant screen prints with water–based inks while benefitting yourself, your family (if printing at home), your students (if on campus), your staff (if printing commercially) and of course, the environment.
Explore these tips for good housekeeping when screen printing, whether you’re printing commercially, on campus or at home.
This article looks at different methods used to keep fabrics in place and some of the issues associated with each of them.
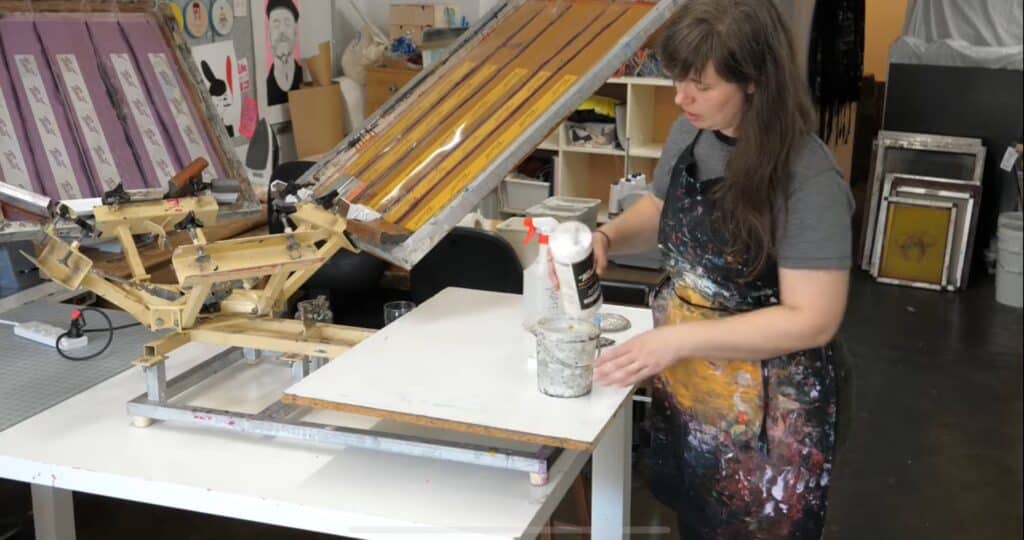
RESTRICTING THE MOVEMENT OF FABRIC
When printing textiles or fabrics, particularly multicolour jobs where tight registration is important, a critical requirement is that there is no movement in the position of the item being printed from the first colour to the last. Even with single colour prints, movement of the substrate under the squeegee for example may yield a fuzzy print.
There are different approaches to restricting movement of the fabric/substrate when screen printing and these are outlined below
ELEI PRINTING
Typically, fabric pieces are held in place with pins around the edge. While this is low cost and chemical free, it is enormously time consuming and limits how close to the edge of the fabric piece the stencil/design can be positioned or applied.
Most printers opt to use a table or platen adhesives instead to hold fabrics in place and dramatically speed up production.
AEROSOL SPRAY ADHESIVE
By far the most common approach used by T-shirt printers is to use an aerosol spray adhesive. As with all things in life, there are upsides and downsides.
Perhaps the biggest advantage of spray adhesives is the convenience of being able to just grab a can, give it a good shake and improve the tackiness of your T-shirt platen, yardage table or other undersurface. Certainly, in the short term, there is no waste (apparently) and the process is relatively (and again apparently) mess free. So, convenience and cleanliness are the drivers.
On the downside, the most obvious disadvantages are emissions of propellants and/or hydrocarbon solvents that end up in the atmosphere as greenhouse gases (GHGs), plus the relatively high ratio of packaging to content. When you discard the aerosol can, there’s likely to be a bit of unused adhesive, propellant and solvent inside, the container is metal, the spray top is plastic which means that even if these cans are sent for recycling, it’s not going to be a simple process…..although that is better than sending the empties to landfill.
Look more closely and over a longer period some more insidious downsides become apparent. When you spray, not all of the adhesive gets onto the platen/print table. Some particles of adhesive end up on the carousel or other housing, but others remain in the atmosphere of the workplace and can be inhaled by operators, which is not good for them, or drift further afield and start to deposit on other items around the print room.
Over the longer term, adhesive deposits can build up on permanent installations like fan blades, beams and rafters making them ready recipients for random airborne textile fibres, lint or dust that starts to accumulate as shop moss.
As well as being unsightly, these shop moss festoons can be havens for the establishment and growth of mould colonies in the workplace and these in turn can wreak havoc with worker health and ink hygiene. Particularly if you’ve already made the leap to printing with water-based inks, a source of falling mould spores in the workplace will increase the likelihood of ink spoilage.
NON AEROSOL TABLE ADHESIVE
Alternatives to spray adhesives include PERMASET® Table Adhesive – a specially formulated non-toxic, non-flammable, water-based pressure sensitive adhesive, ideal for use in fabric printing. When applied, PERMASET® Table Adhesive provides a thin tacky film that holds the print in place, eliminating movement of the fabric during and between prints, essential for multi-colour prints where tight registration is critical or for holding fabric in place during Elei printing.
PERMASET® Table Adhesive can be applied by:
- Spray—using PERMASET® Table Adhesive at full strength or up to 50% dilution with water in a spray bottle will most closely match the convenience and cleanliness benefits associated with the use of aerosol spray adhesives. A downside of spray application, common to all spray adhesive applications, is that issues associated with airborne aerosol particles remain, as outlined above for spray-can adhesives. Another downside is that, particularly in cold or humid weather, the newly applied adhesive may take longer to become tacky.
- Brush or roller—What is important here is that the film is of uniform thickness, so there are no ridge lines or brush marks for example that might be telegraphed
- Pour on, squeegee off—pour on and spread out with a plastic or rubber blade (or a credit card as shown above). This technique is most appropriate for rubber or vinyl coated surfaces and requires only sparing amounts of table adhesive. An area of wet adhesive the size of a small coin (1 cm; ½”) will comfortably cover an entire platen. This is also the most economical, least wasteful application method and leaves the cleanest, smoothest adhesive film.
Once dry, the table adhesive film is water resistant and remains tacky for extended periods. PERMASET® Table Adhesive can even be reactivated by spraying with water and allowing to stand for a few minutes.
As noted above, a downside of water-based adhesives is that they do not flash off as quickly as solvent based adhesives and this is particularly relevant in cold and/or humid environments.
A common perception is that the tackiness of water-based adhesives is not as aggressive as the solvent based adhesives in spray cans. However, a number of printers who’ve used both, claim that the obverse is true. That is, they find water-based adhesives to have more aggressive tack, not less. If it’s too tacky, then just use less.
Using alternatives to spray adhesive in your print practice is part of good hygiene and housekeeping practice that will help you produce sharp, bright prints and maintain a healthy working environment for yourself, your staff, perhaps for your students and definitely for the planet.
©COLORMAKER INDUSTRIES 2024.
Subscribe to get the latest inspiration, news & advice direct to your inbox
More articles
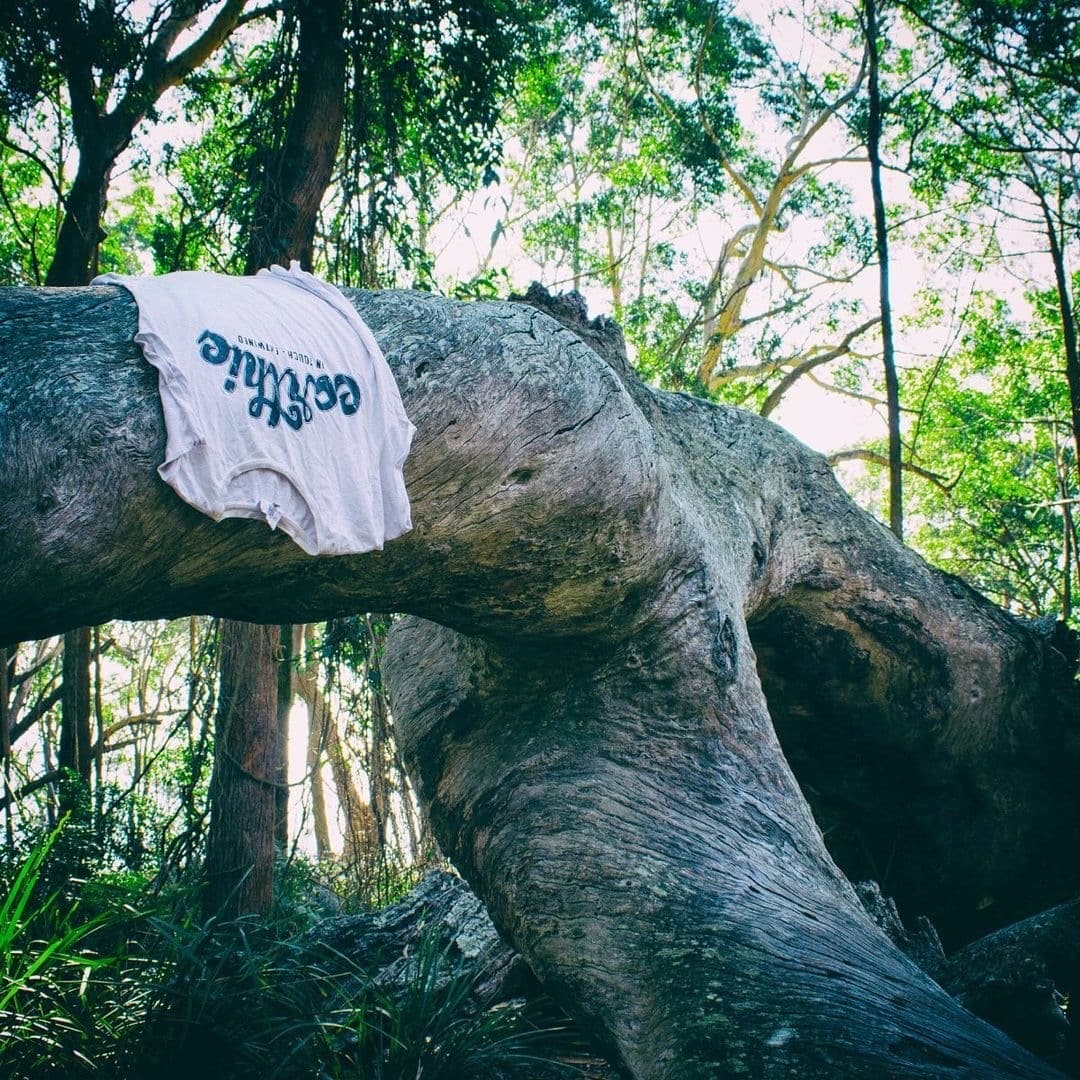
Clothing label I’m Earthie shares how they strive to be a truly sustainable brand
Clothing label I’m Earthie shares how they strive to be a truly sustainable brand