Projects, tips & ideas to keep you inspired
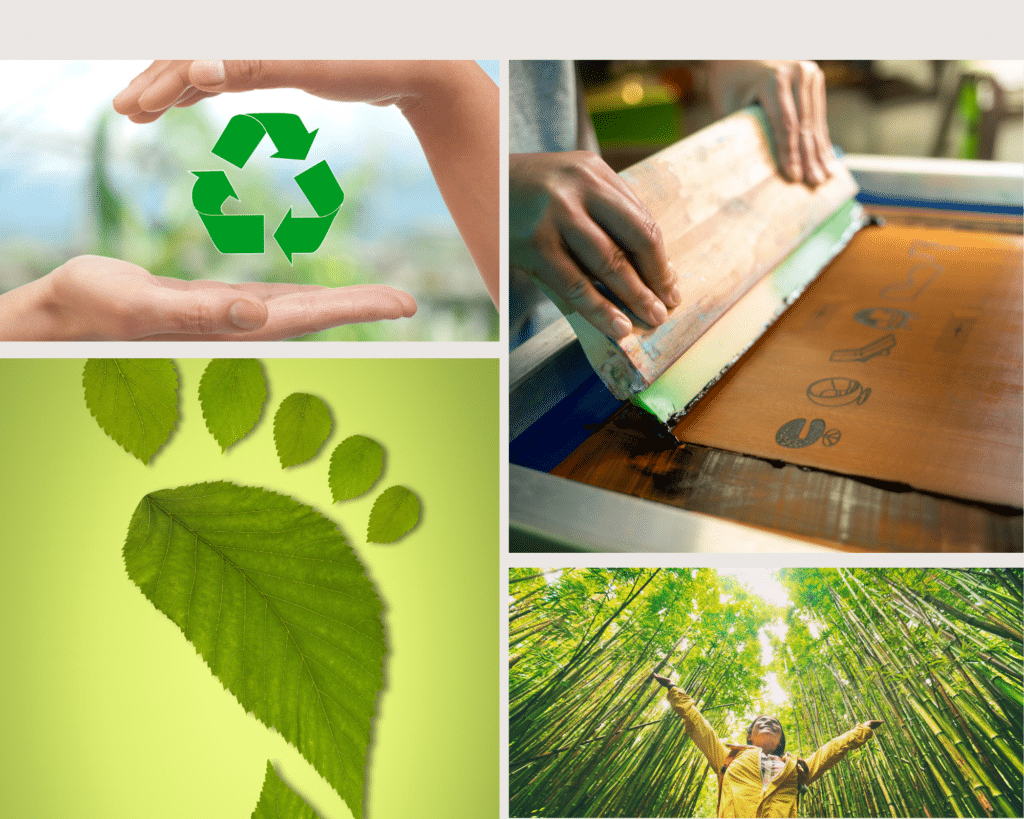
Eco-friendly Screen Printing: A Guide for Artists and Printers
Eco-friendly Screen Printing: A Guide for Artists and Printers
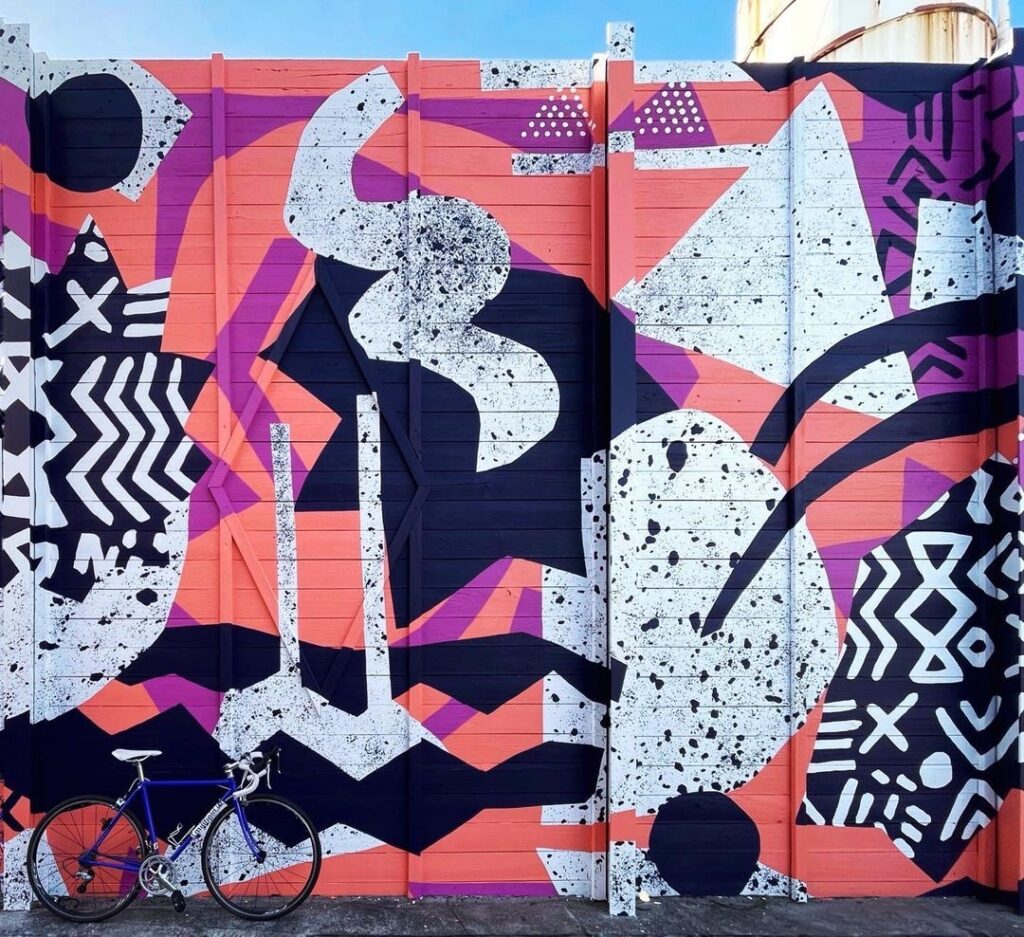
Getting started on a street beautification project
Getting started on a street beautification project
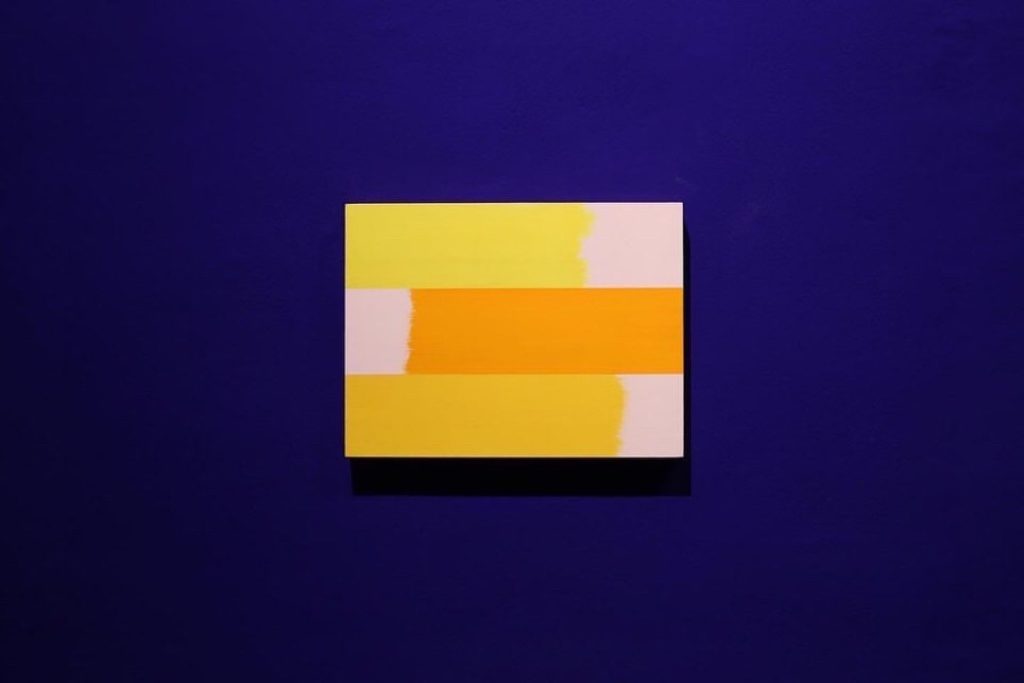
Abstract Realities Exhibition used PERMACRYLIK Paints as Part of the Artwork
Abstract Realities Exhibition used PERMACRYLIK Paints as Part of the Artwork
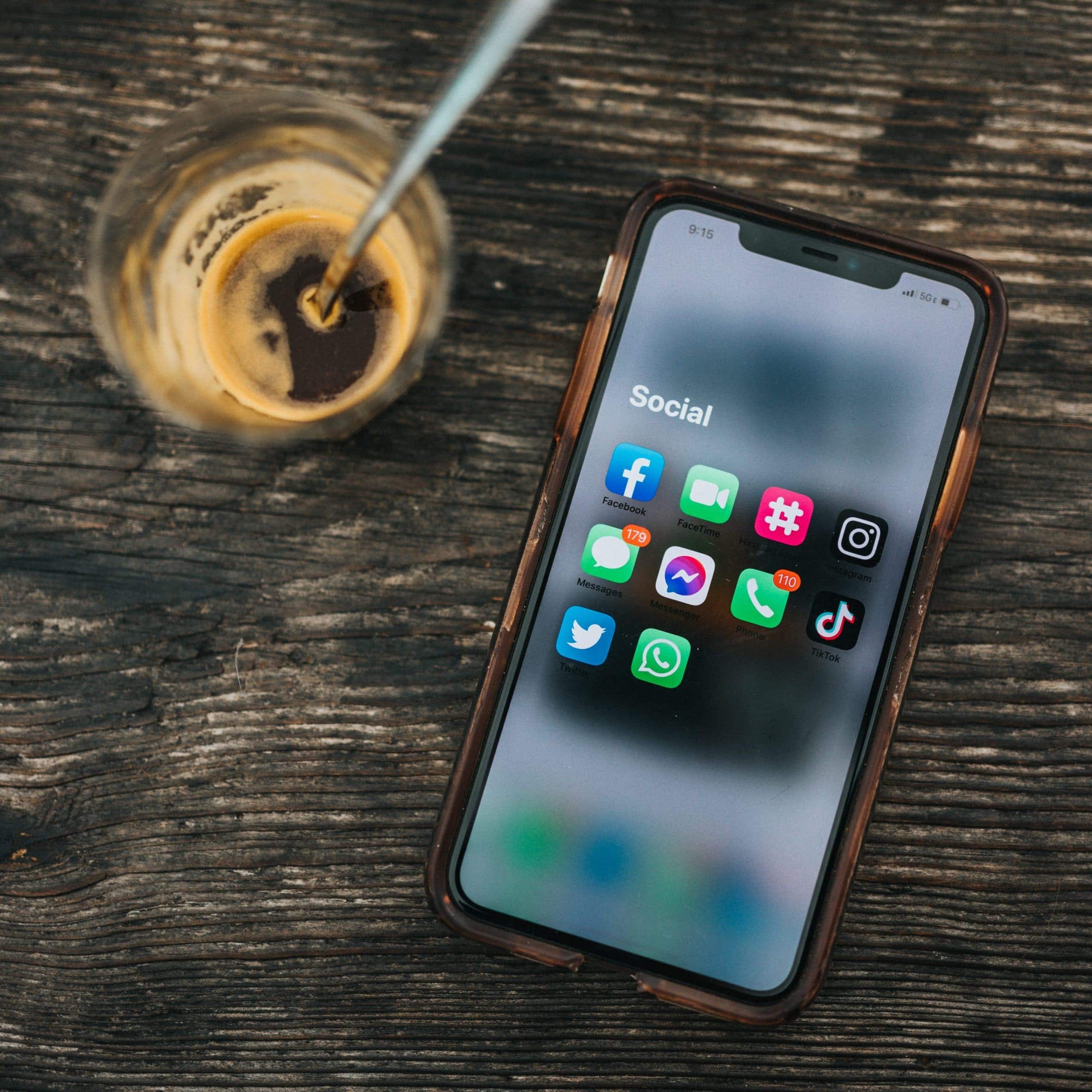
The handy guide to marketing your screen printing business on social media
The handy guide to marketing your screen printing business on social media
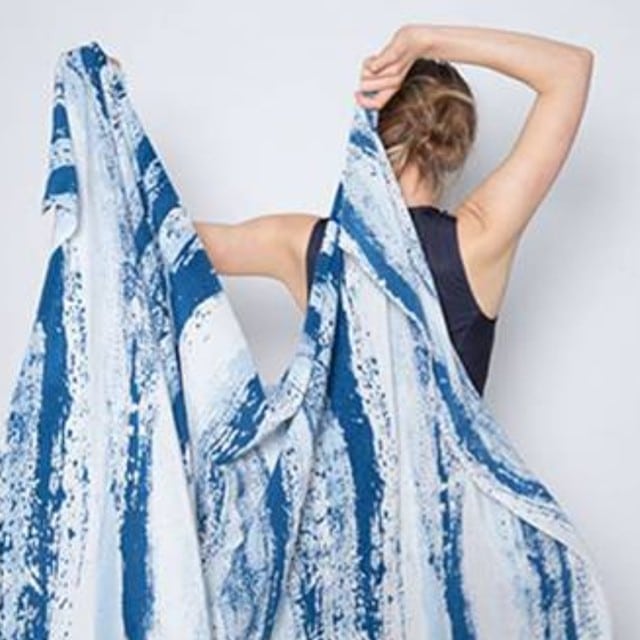
How to screen print on different kinds of fabrics
How to screen print on different kinds of fabrics
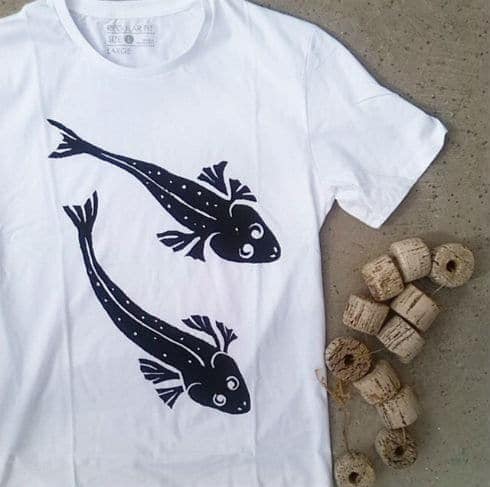
How to screen print your own T-shirt in 6 easy steps
How to screen print your own T-shirt in 6 easy steps
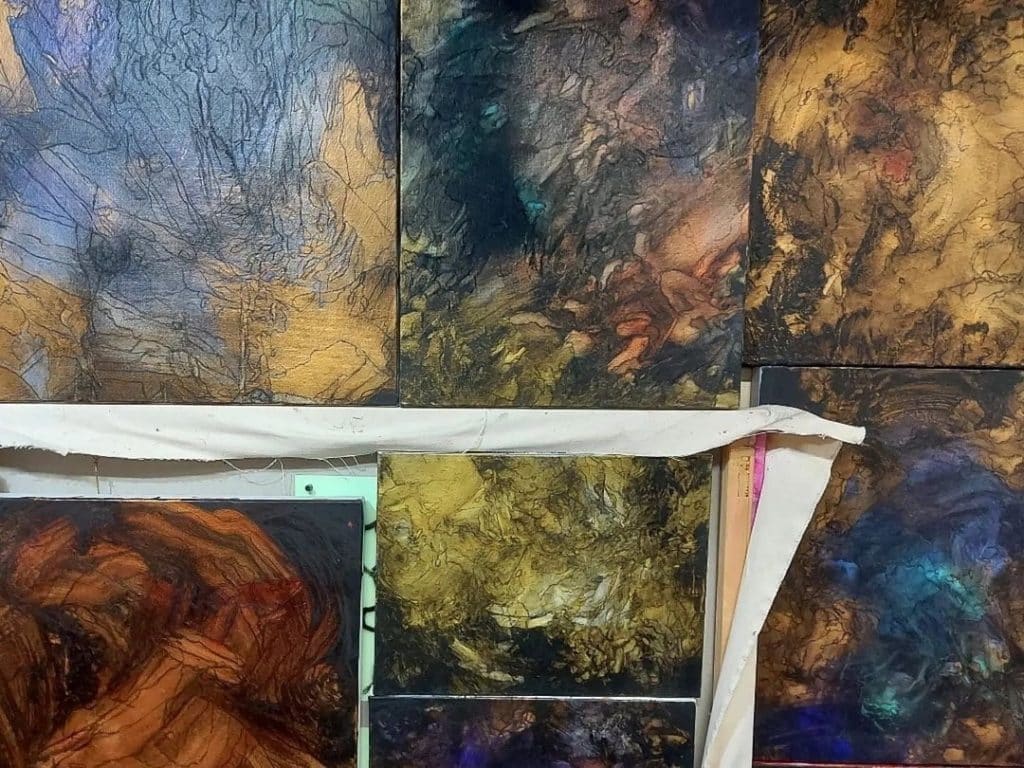
Artist Kade Valja Explores Energetic Forces using PERMACRYLIK Scenic Paints
Artist Kade Valja Explores Energetic Forces using PERMACRYLIK Scenic Paints
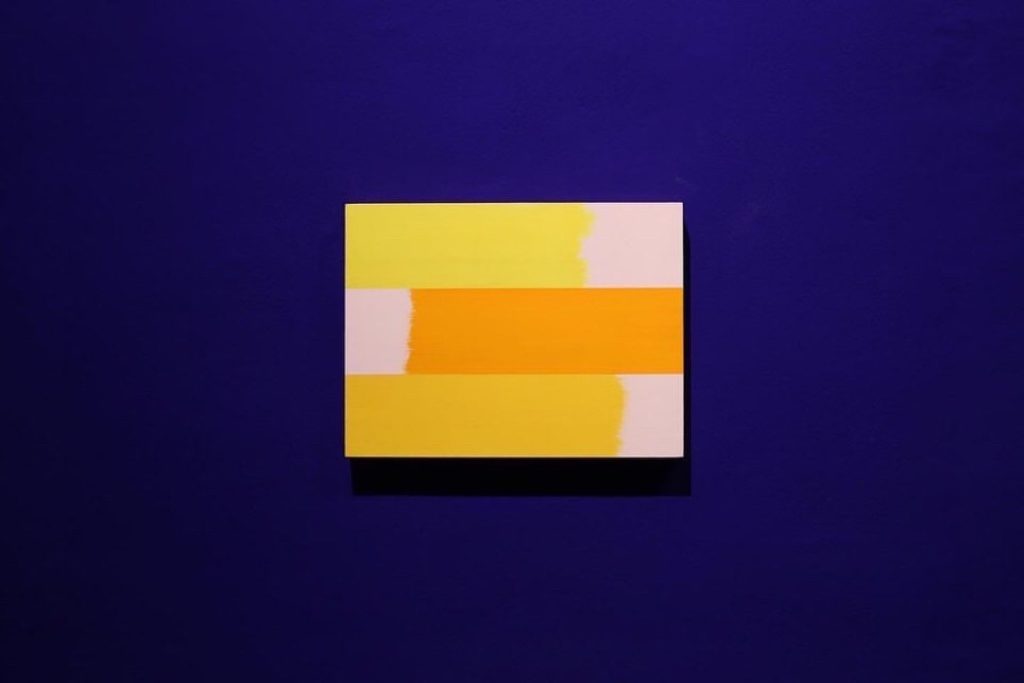
Abstract Realities Exhibition used PERMACRYLIK Paints as Part of the Artwork
Abstract Realities Exhibition used PERMACRYLIK Paints as Part of the Artwork
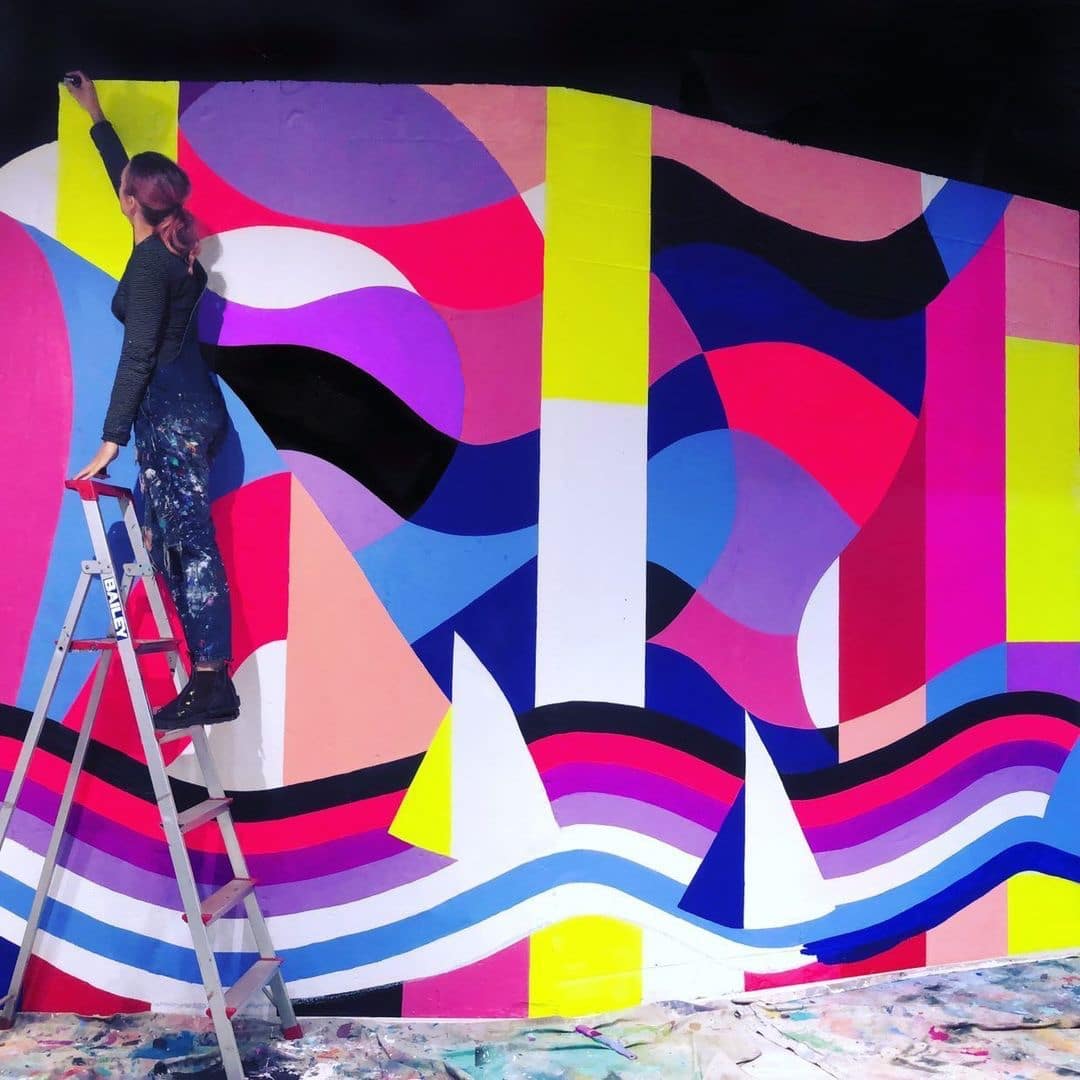
Creating a wall mural: Beginner scenic painting techniques explained
Creating a wall mural: Beginner scenic painting techniques explained
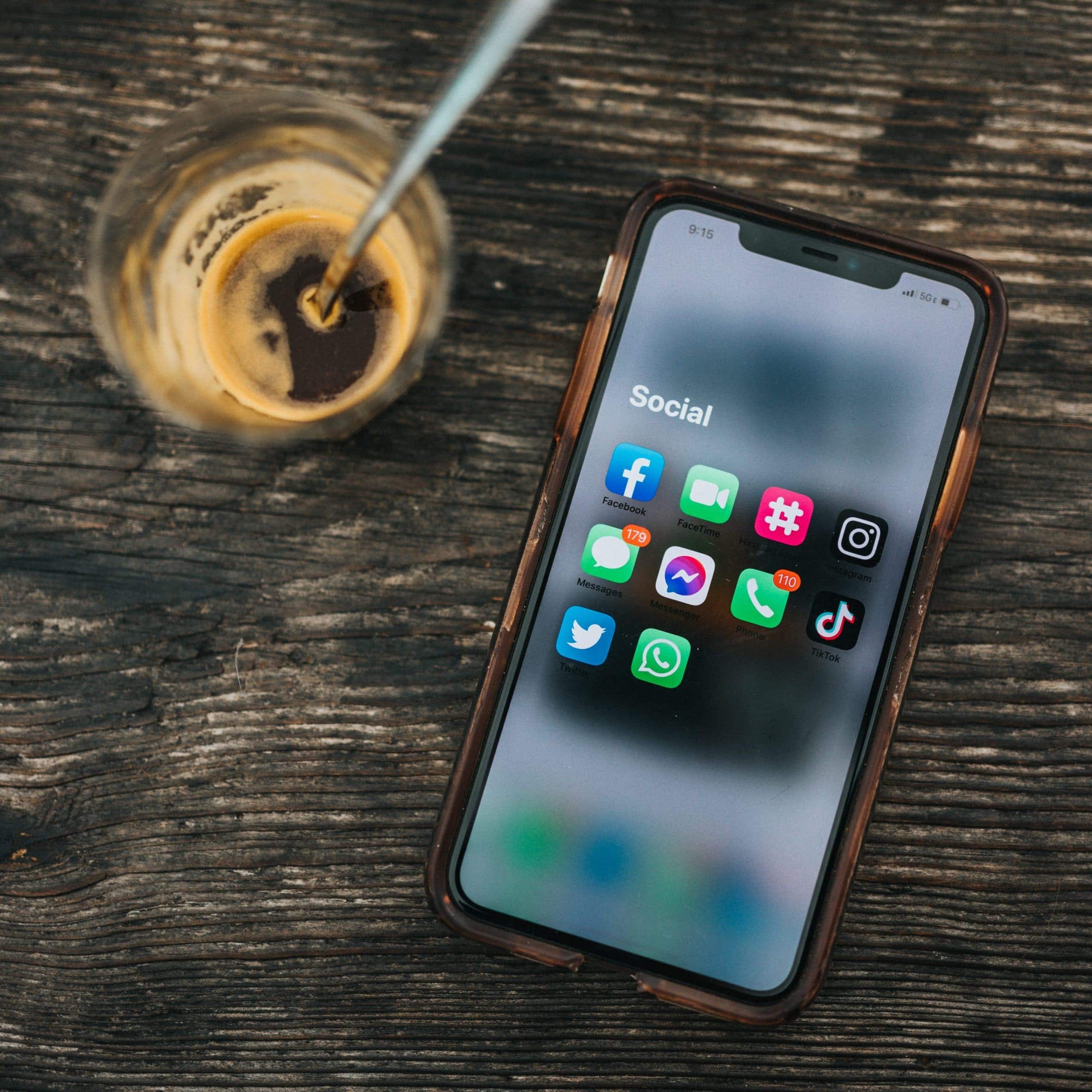
The handy guide to marketing your screen printing business on social media
The handy guide to marketing your screen printing business on social media
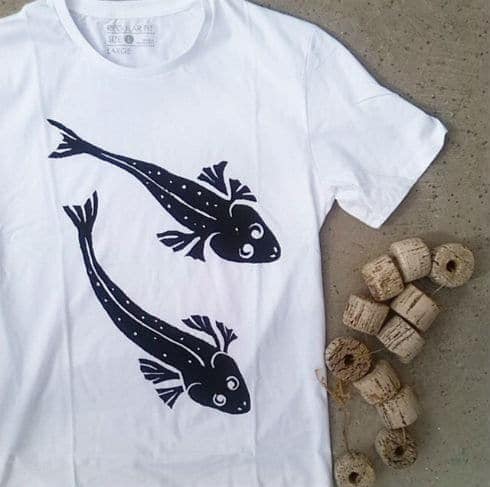
How to screen print your own T-shirt in 6 easy steps
How to screen print your own T-shirt in 6 easy steps
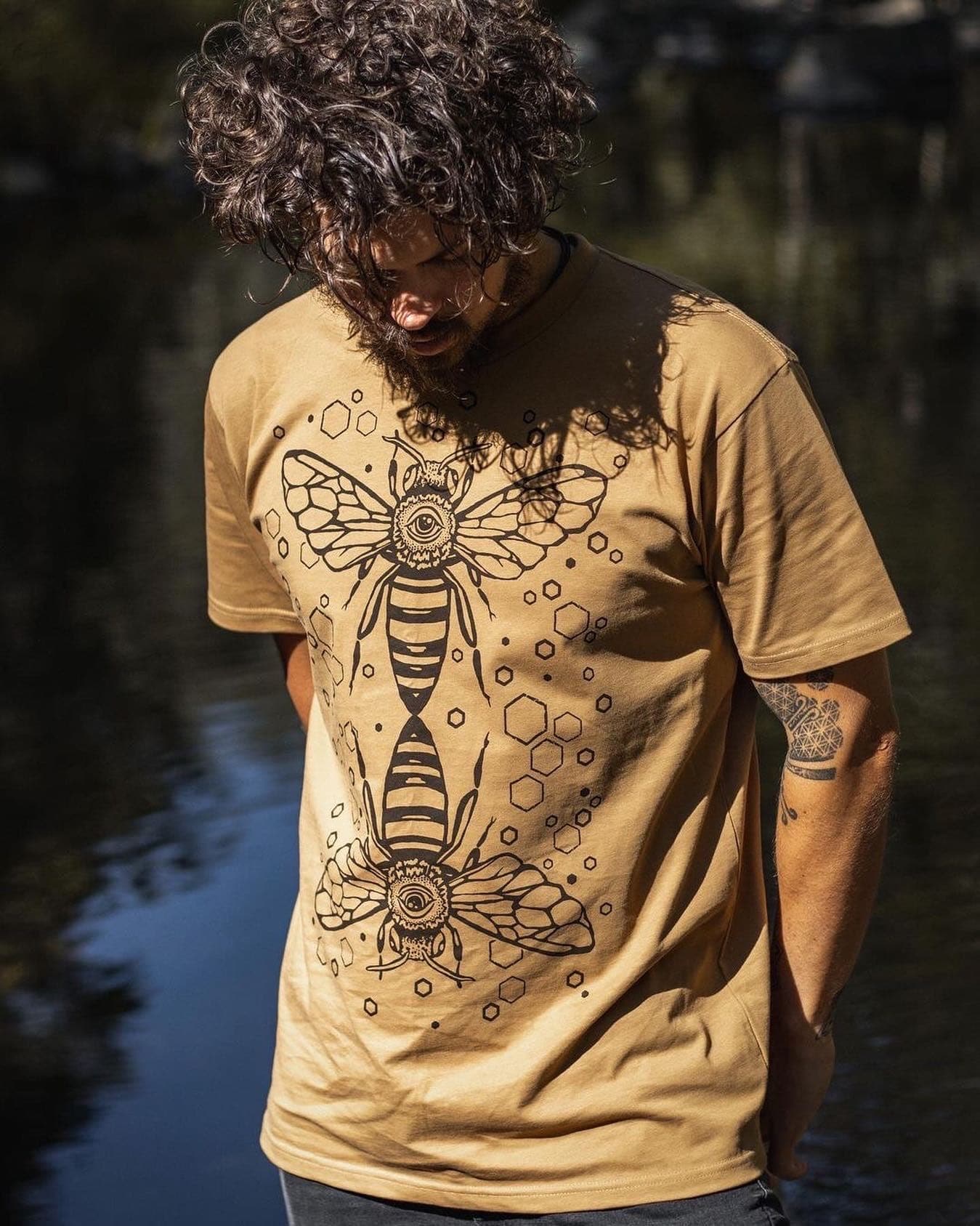
How to screen print organically: Finding supplies in 2022
How to screen print organically: Finding supplies in 2022
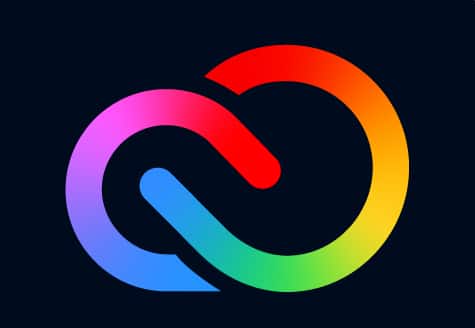
Check out 5 fabulous apps for designing T-shirts
Check out 5 fabulous apps for designing T-shirts
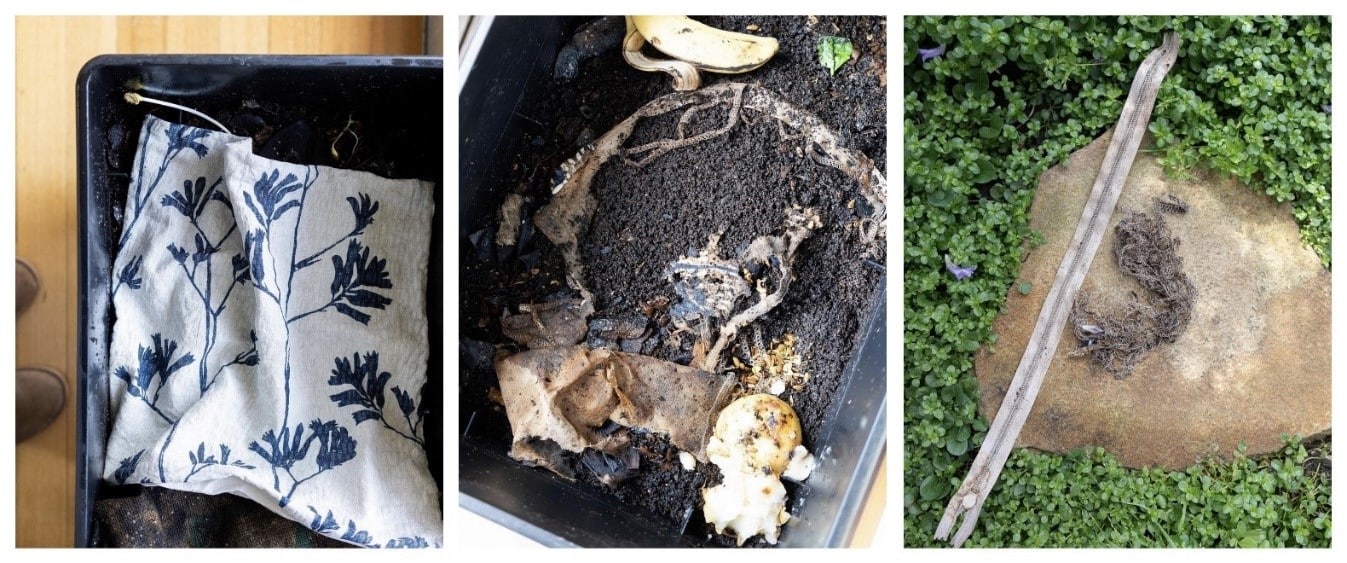
Are PERMASET screen print inks compostable?
Are PERMASET screen print inks compostable?
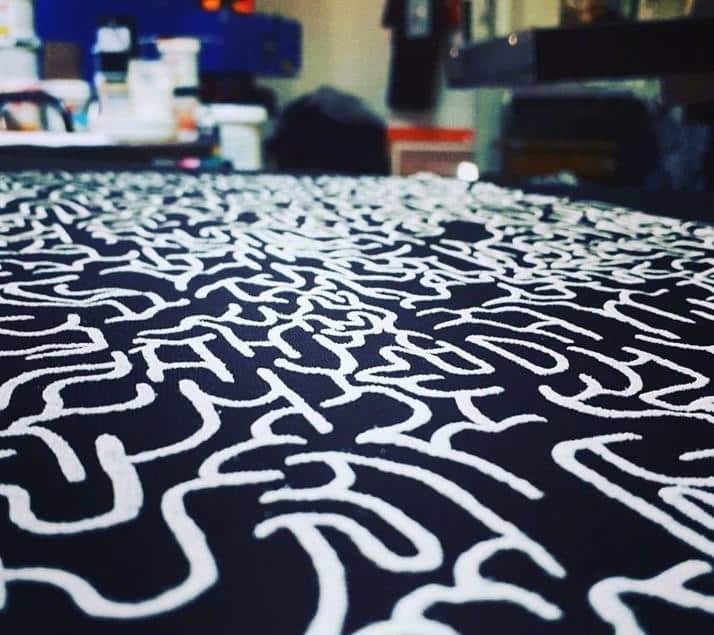
How to make custom 3D prints using PERMASET Puff Paste
How to make custom 3D prints using PERMASET Puff Paste
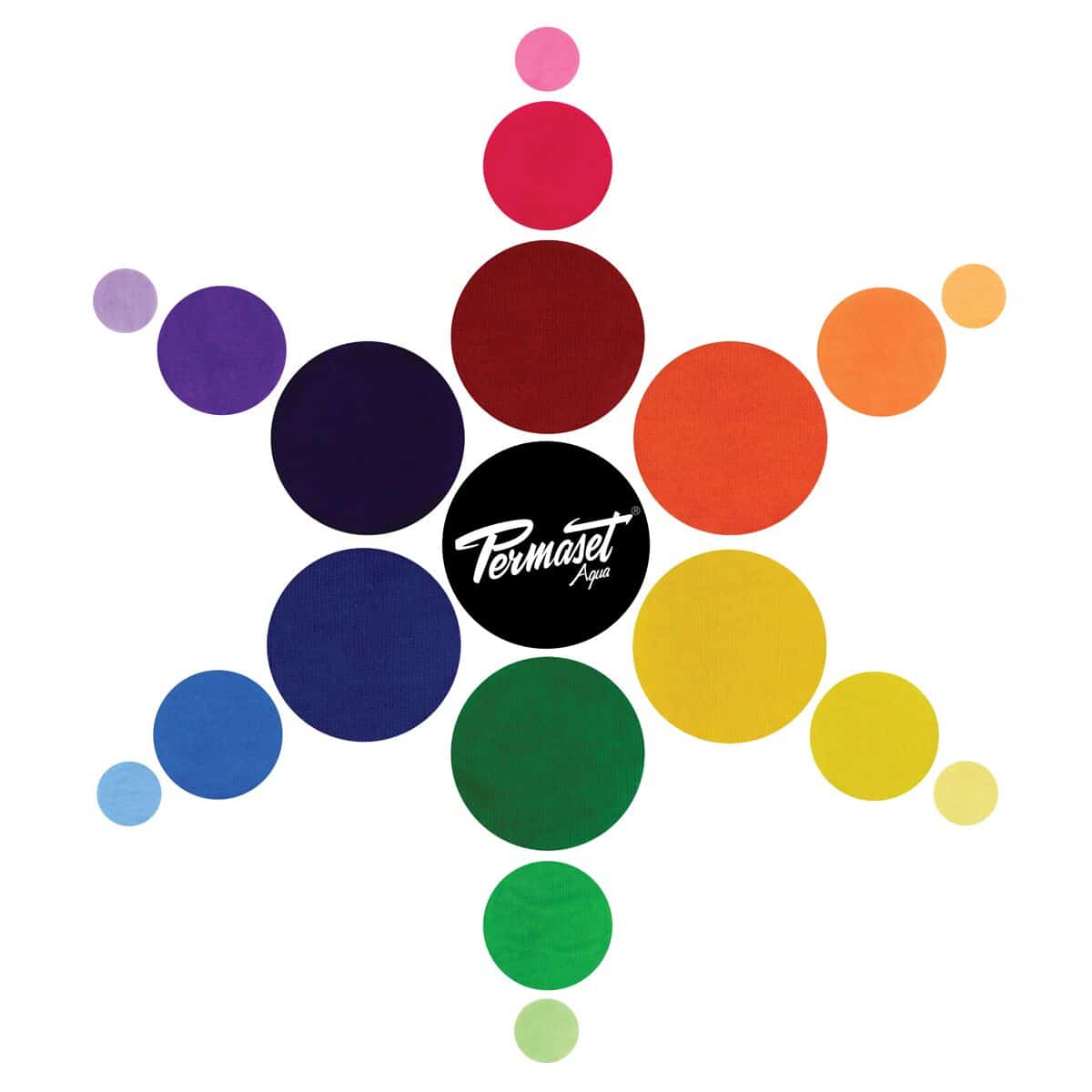
Getting to know PERMASET textile screen printing inks: Working with colour (Part 2)
Getting to know PERMASET textile screen printing inks: Working with colour (Part 2)
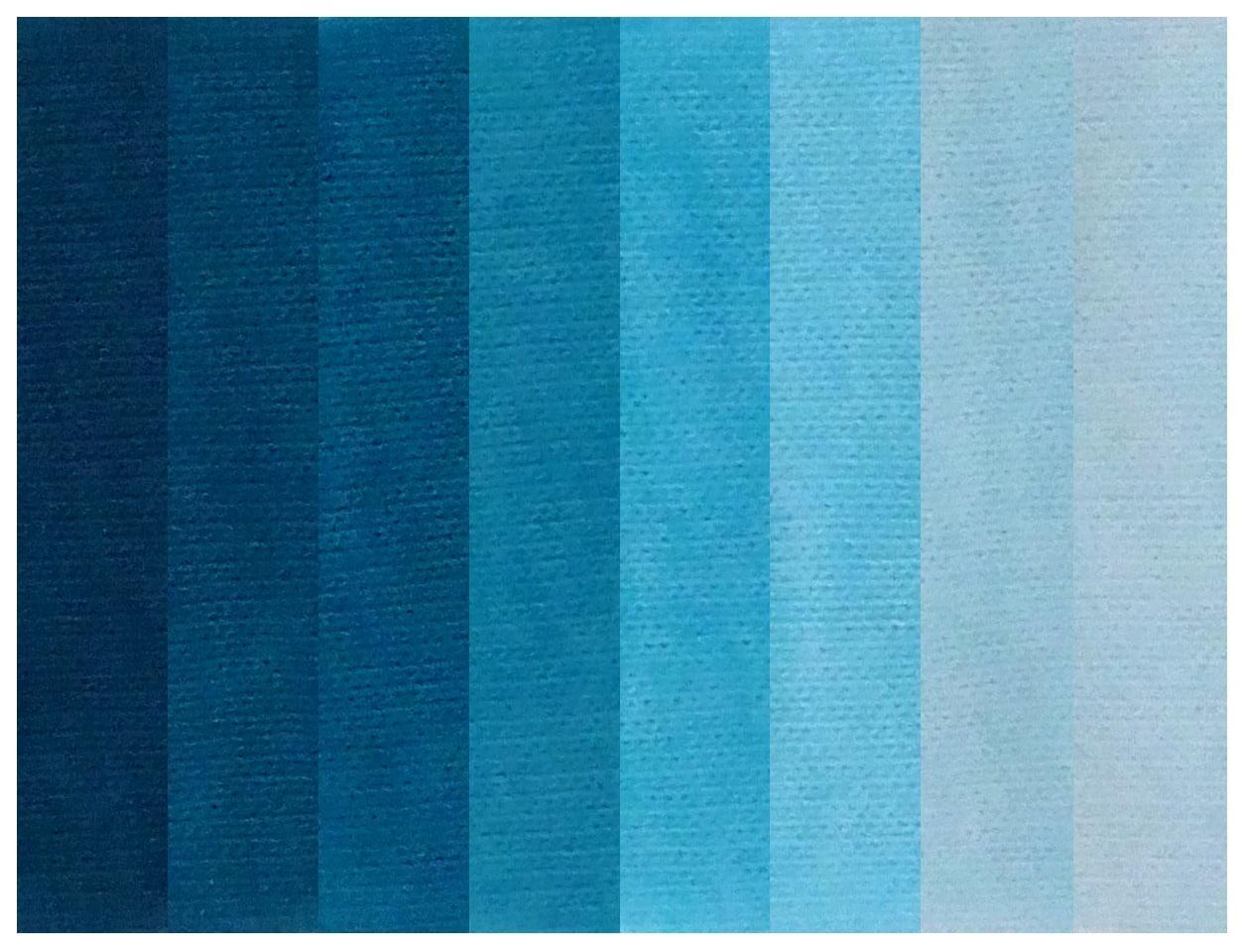
Getting to know PERMASET textile screen printing inks: Working with colour (Part 1)
Getting to know PERMASET textile screen printing inks: Working with colour (Part 1)
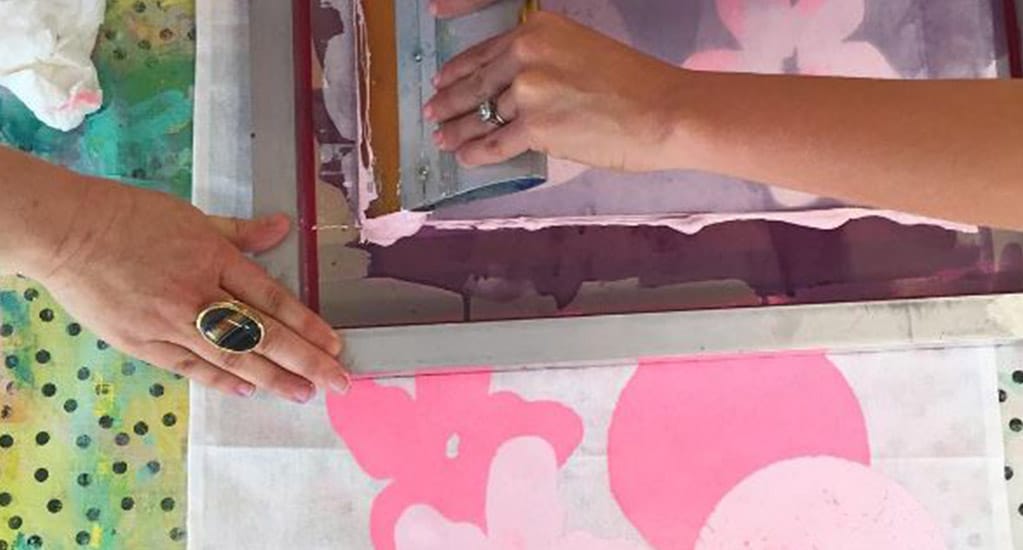
How to start screen printing at home
How to start screen printing at home
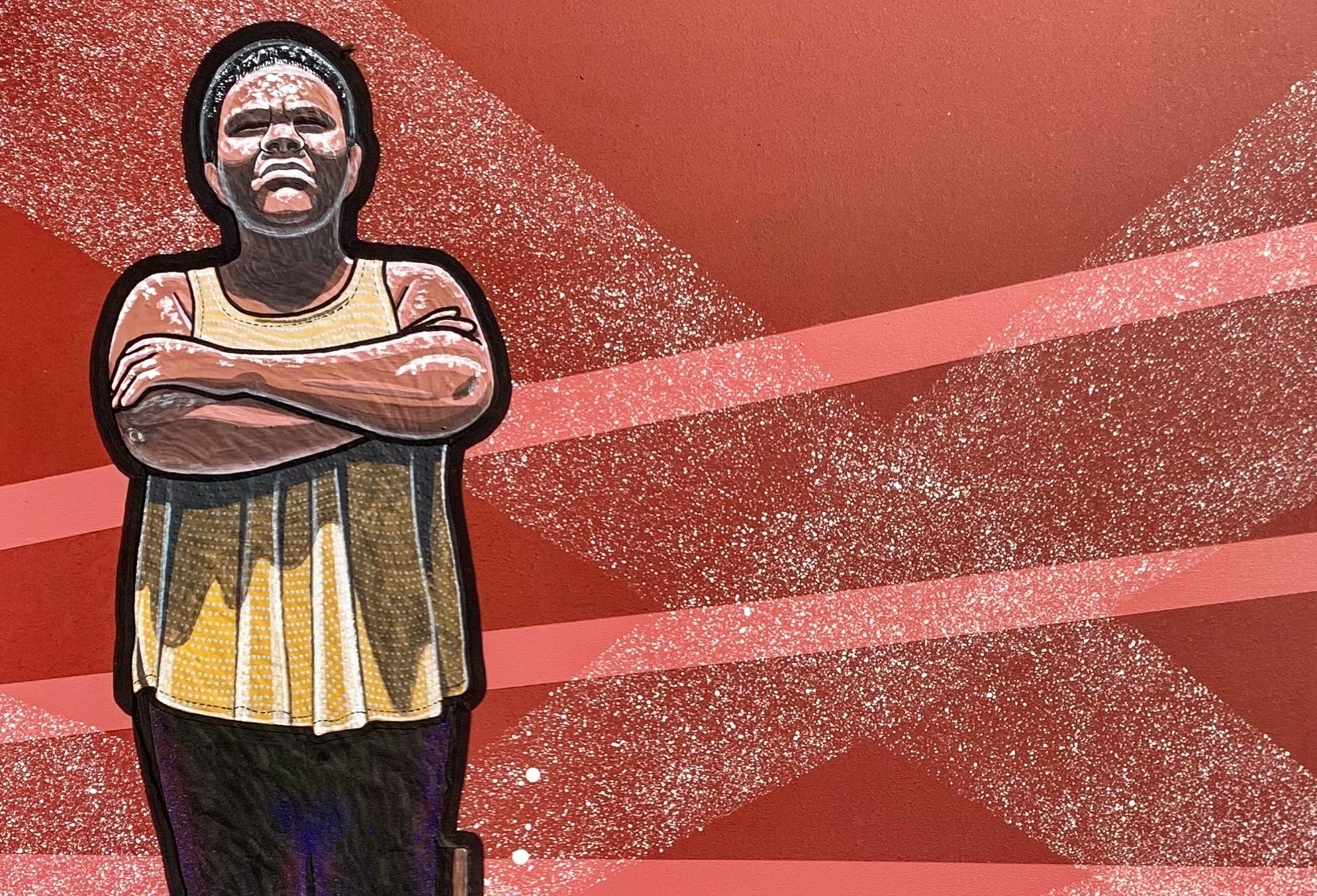
Hear how celebrated indigenous artist, Blak Douglas won the 2019 Kilgour Art Prize
Hear how celebrated indigenous artist, Blak Douglas won the 2019 Kilgour Art Prize
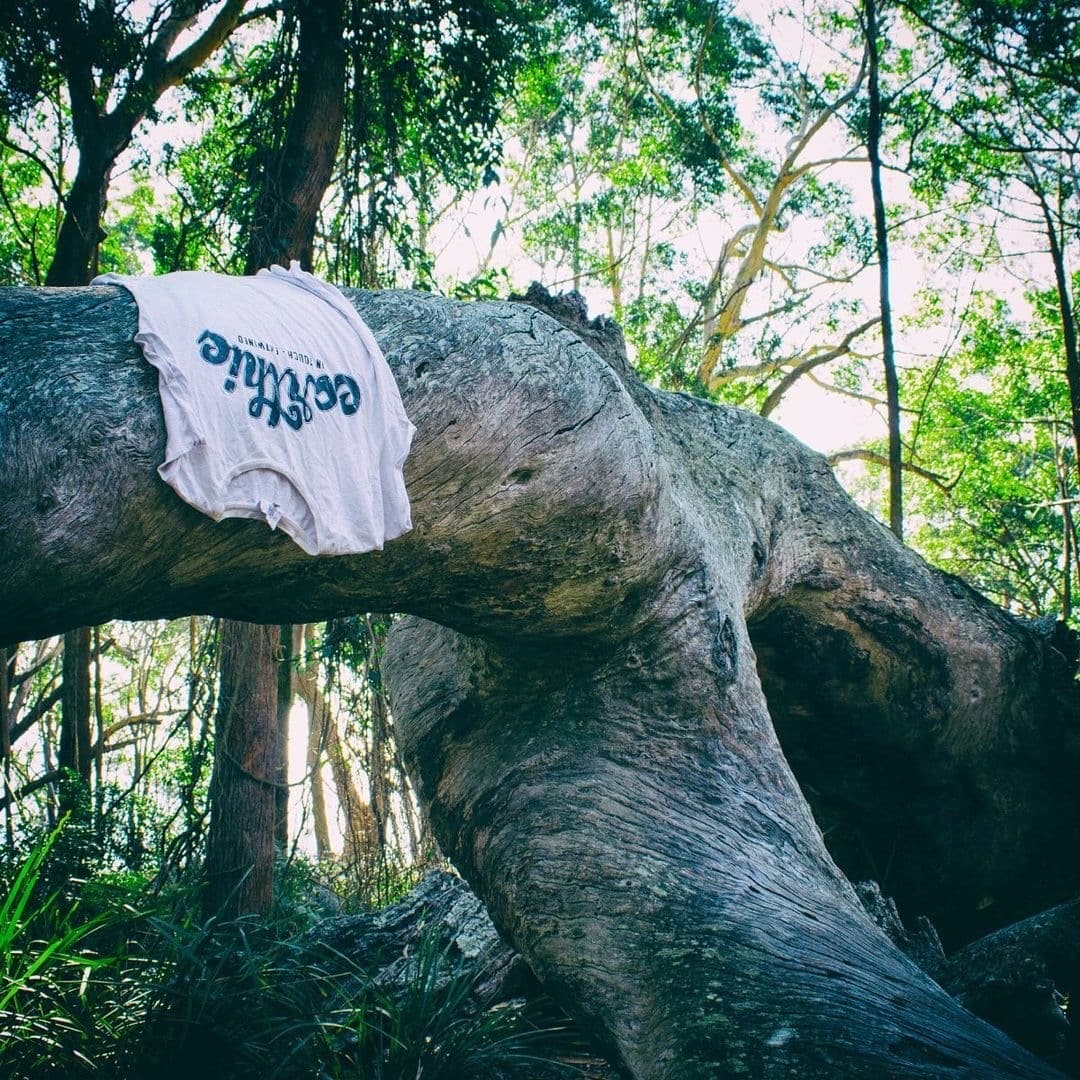
Clothing label I’m Earthie shares how they strive to be a truly sustainable brand
Clothing label I’m Earthie shares how they strive to be a truly sustainable brand
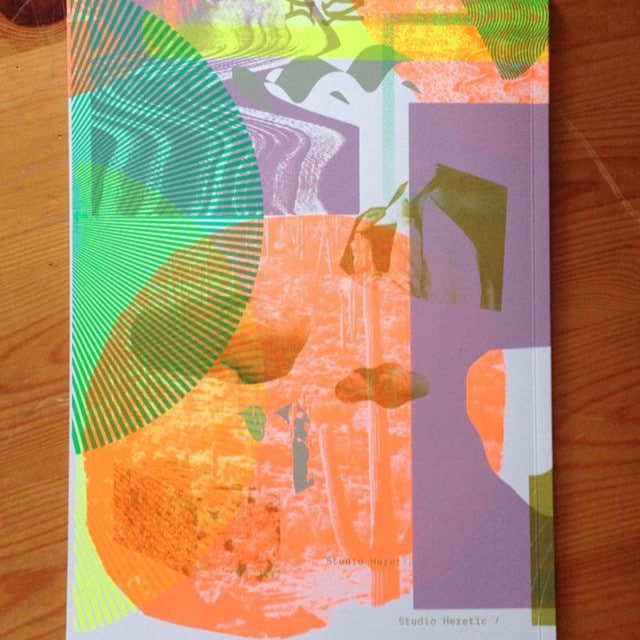
Hear how Heretic Printmakers UK printed magazines using PERMAPRINT Premium Inks
Hear how Heretic Printmakers UK printed magazines using PERMAPRINT Premium Inks
Hand printed block patterns
Read this helpful blog providing technical advice about how to block print using PERMASET Inks
Hand painted clothing
Learn practical tips and see examples of painting on fabric to create T-shirts, dresses, yardage, canvas artworks, bags and even shoes using PERMASET Inks
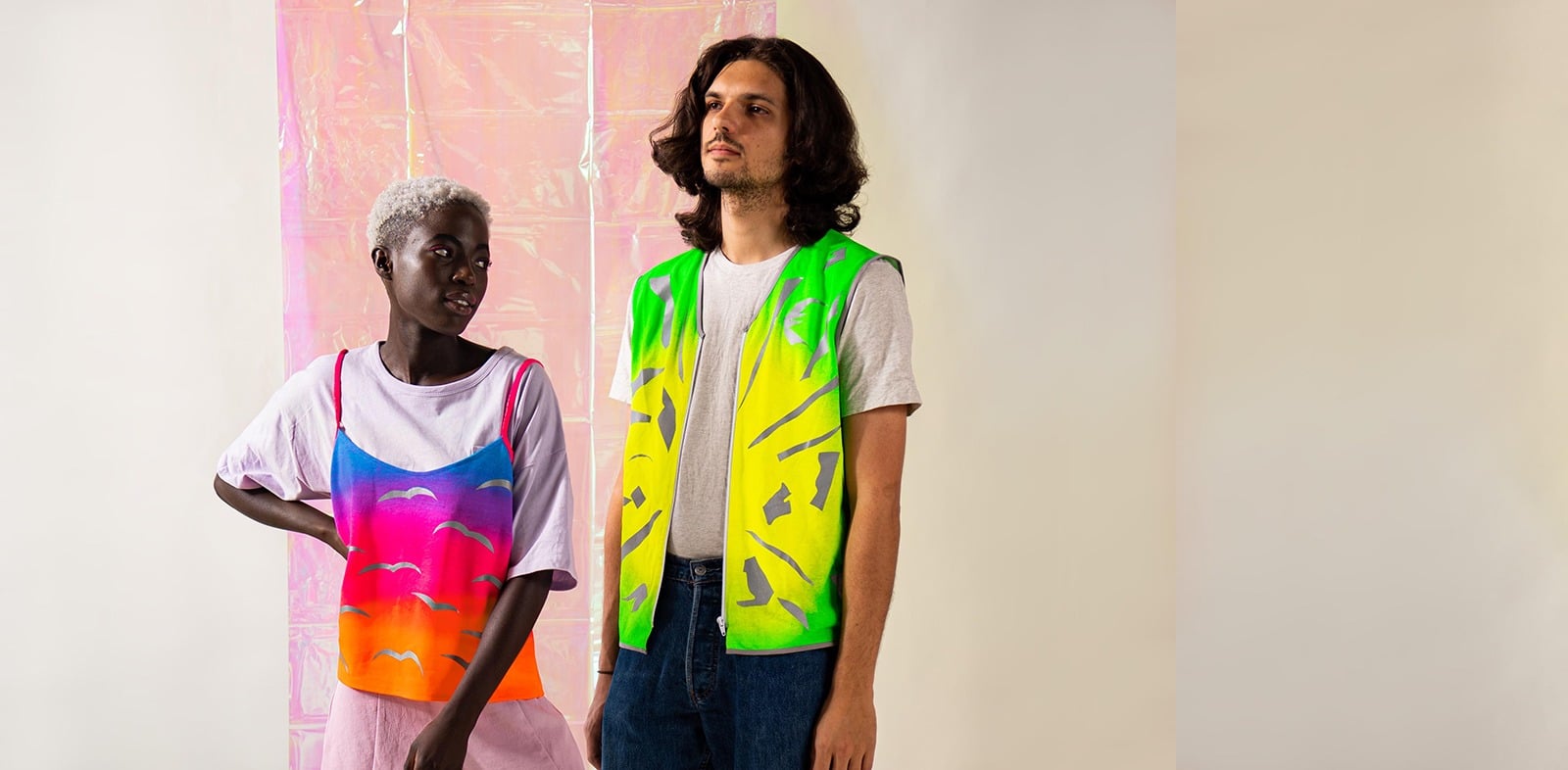
Meet the artists
This month we meet HEY REFLECT’O & see how PERMASET Ink has helped create their vision
Subscribe to get the latest inspiration, news & advice direct to your inbox
Learn how other printers are using water-based inks
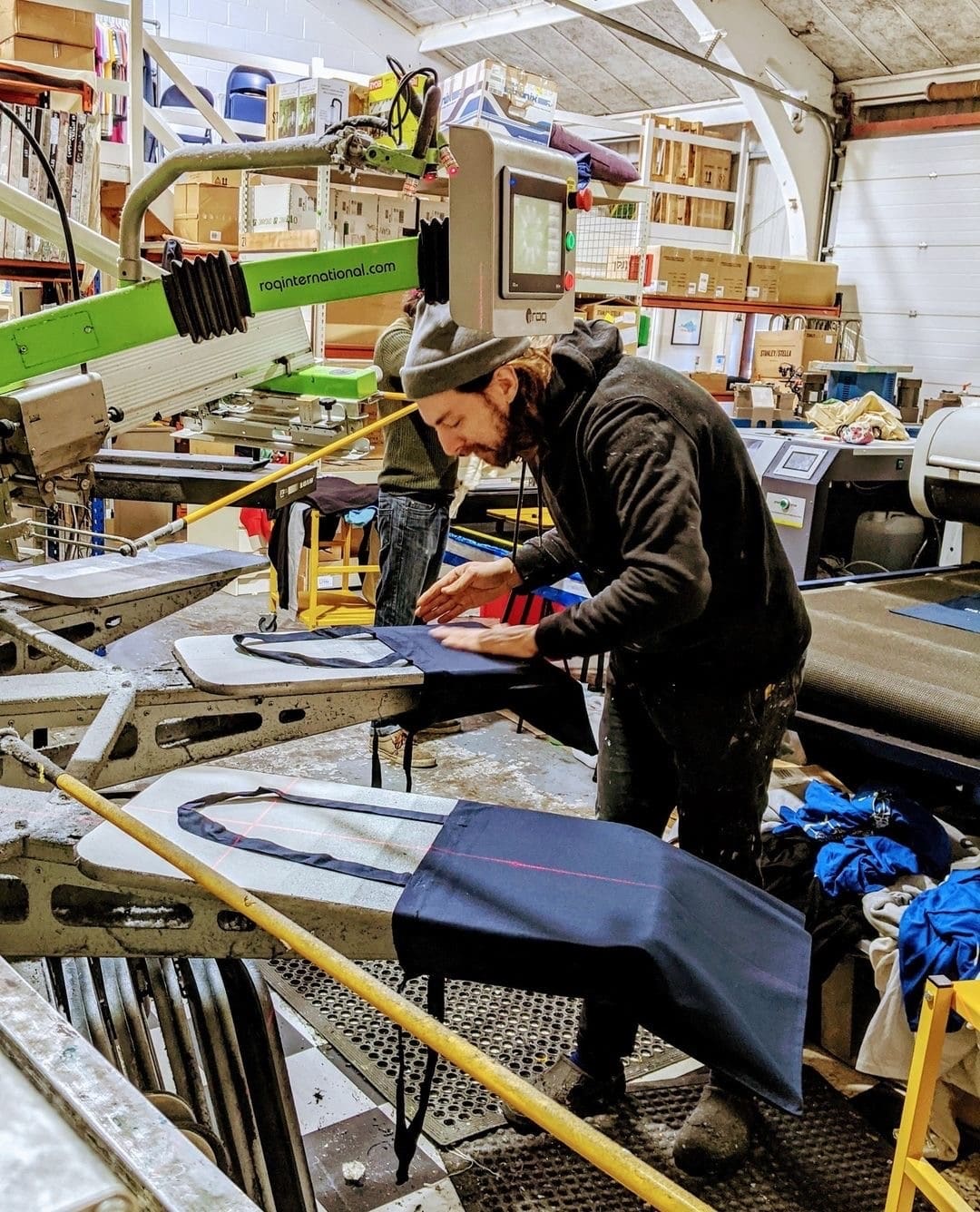
Hear how I Dress Myself print shop has used water-based inks in their ethical business
Hear how I Dress Myself print shop has used water-based inks in their ethical business